Главная страница сайта
Российские промышленные издания (узловые агрегаты)
1 ...
13 14 15 [
16 ]
17 18 19 ...
24 клонений от правильной формы поверхностей подшипника и вала (овальность, конусность, корсетность) и микронеровпостей указанных поверхностей соприкасаются выступающие части этих неровностей, что характеризует переход в область полусухого трения.
Отношение минимальной толщины слоя смазки к критической толщине называется коэффициентом надежности подшипника:
у llllll
(1111п)кр
Коэффициент надежности возрастает с уменьшением удельного давления fecp, увеличением вязкости ц и 5величением числа оборотов п.
Наиболее эффективными средствами увеличения коэффициента надежности являются:
1. Увеличение числителя hm главным образом за счет правиль ного выбора параметров fecp, ц и ю. определяющих приведенную выше безразмерную нагрузку ij)fecp/n i, а также за счет хорошего отвода тепла от подшипника путем принудительного прокачивания масла через зазор, что предохранит от резкого снижения вязкости при повышении температуры масла. Только при эффективном охлаждении подшипника можно идти на увеличение Атш за счет увеличения оборотов, так как тепловыделение на единицу поверхности подшишшка пропорционалыю квадрату числа оборотов, а следовательно, с ростом числа оборотов будег уменьшаться вязкость смазывающей жидкости.
2. Уменьшение знаменателя (/гт1п)кр за счет увеличения точности и чистоты обработки вала и подшипника и тщательной фильтрации смазывающей жидкости.
Для обеспечения режима жидкостного трения необходимо под держивать в определенных пределах не только минимальную толщину слоя, но и температуру полншпника. Послелняя зависит в основном от работы трения, температуры и количества протекающей через подшипник жидкости.
Момент трения можно найти следующим образом.
Из табл. 3 находим безразмерную величину Ж^ф/рс/цСц в зависимости от относительного эксцентриситета х и отношения /ц/Оц, а затем, зная геометрические параметры - диаметр и длину цапфы
и 1ц, относительный зазор скорость v и вязкость ц, находим момент трения М.
Момент трения определяется по средней вязкости, соответствующей средней температуре между температурами входящей жидкости и подшипника. Эта средняя температура приблизительно равна температуре выходящей из подшипника жидкости.
Найдя момент трения М, можно определить:
1. Мощность трения
=Mui кГм1сек=- л. с.
Таблиц а 3 Значения бевразмерного отношения MftwluD
| |
0,33 | | | |
| | | 3,55 | |
| 3.95 | | | 4,35 |
| | | | |
| | 5,55 | | |
0,85 | 6,25 | | 7,05 | |
| 7.75 | | 8,85 | |
0,95 | 11.25 | 11.9 | 13.0 | 13,6 |
0.97 | 15,0 | 16,0 | 16,7 | 17,5 |
0,99 | 27,8 | 29,0 | 30,75 | 31,4 |
0,995 | | 42,6 | 44,7 | 45,4 |
2. Количество тепла, эквивалентное этой мощности;
3. Количество жидкости, которое надо прокачать через подшипник для отвода всего тепла трения Qip. Эта величина определяется из равенства
где Д<=4ы1-вх-повышение температуры прокачиваемой через подшипник жидкости; с - средняя теплоемкость 1 л жидкости. Для случая подвода смазки в круговую канавку, расположенную на конце подшипника, количество прокачиваемой через подшипник жидкости Qn (в л/мин) определится по формуле
Q =0,16(l + ).5y3--
где 6к - ширина канавки;
Оц и /,[ -диаметр и длина цапфы в мм;
Рк - давление жидкости в канавке в кГ/см; 6 - радиальный зазор в мм; Ивых - абсолютная вязкость выходящей жидкости в кГ-сек/м'.
Расчет рессоры
Расчет рессоры ведем на касательные напряжения, возникающие при передаче крутящего момента. В связи с колебаниями величины крутящего момента, эти напряжения будут переменными с асимметричным циклом. Коэффициент асимметрии цикла равен отношению наименьшего напряжения цикла к наибольшему
j. , Tinin Alijn (202)
т,ах Almax
Найдем величину Гц на основании сделанного ранее вывода о величине пульсации расхода.
Для обычного качающего узла величина пульсации расхода равна:
9 4(2гЛ-ЬЛ2) 4(г-Ц)
= 1-0,. (203)
Считая поток турбулентным, получим, что отношение давлений равно квадрату отношения расходов, т. е.
Ртах Vmax /
Но так как мощность и крутящий момент пропорциональны про изведению pq, то коэффициент асимметрии цикла
j. Jmlil Pmlngniln / 1т\а -(1 о ) (204)
Л^тах Pmax9niax Vgmax /
Следовательно, для обычной схемы
4(z-f 1)
(205)
Для схемы двухроторной с соответствующим смещением роторов
.6(.+l)J (°>
в действительности пульсация дав.пения, а следовательно и крутящего момента, будет меньше величин, определяемых приведен- ными формулами, за счет того, что влияние высокочастотной пульсации расхода будет в известной степени компенсироваться упругими деформациями стенок каналов и трубопроводов магистрали.
При наличии надежных экспериментальных данных о величине пульсации давления, в формуле для определения отношения Pmin/pmai И величины Гц МОЖНО ввести соответствующий поправочный коэффициент.
Однако считается возможным вести расчет по предлагаемой методике, так как отсутствие этого коэффициента компенсируется тем, что не учитывали изгибных напряжений, возникающих за счет перекосов и песоосности шлицев ведущей шестерни и привода.
Необходимо точностью изготовления шлицев, посадочных мест и их взаимного расположения, а также зазорами в шлицевых соединениях добиться максимального снижения изгибных напряжений.
При наличии дополнительных тангенциальных напряжений, возникающих вследствие крутильных колебаний на режимах, близких к резонансным, рекомендуемый запас прочности может оказаться даже недостаточным.
Если принять за основу расчета схематизированную диаграмму предельных напряжений, очерченную прямыми линиями, то можно определить запас прочности без непосредственного использования диаграммы испытания на усталость.
В приведенных ниже формулах введены следующие обозначения:
-bn>i +min -среднее тангенциальное напряжение цикла;
с Tniin
- амплитуда цикла;
т, -предел текучести, т. е. касательное напряжение, при котором остаточные деформации достигают 0,2%;
т -предел выносливости при симметричном цикле; Т|, -предел выносливости при пульсирующем цикле
(от нуля до максимума); т, -предел выносливости при изменении'напряжений
с асимметричным циклом; ,--эффективный коэффициент концентрации напряжений, представляющий собой отношение предела пьигасливости при си51нетричном цикле без концентрации к пределу выносливости при симметричном цикле с концентрацией; г -масштабный фактор, характеризующийся отношением предела выносливости т , при данных размерах поперечного сечения к пределу выносливости того же материала, получегшому на обычных
лабораторных образцах о [, т. е. е=-=3-;
-и
Д.- коэффициент новерхиостей чувствительности, зависящий от качества обработки поверхности и
характеризующийся отношением, где
-предел усталости при высоком качестве поверхности (полировка, суперфиниш).
Для рессор имеет место неравенство
/т^ jY
где Тт, - среднее напряжение, при котором диаграмма Смита делает перелом (фиг. 61). При соблюдении неравенства (207), запас прочности определяется следующим образом:
Tm-f
.(1 Д)
Найдем соотношение между Гг и Хт-
тяте
(208)
(209)
или, подставляя вместо tmax его значение из уравнения (209), получим
1-f ц
Подставляя значение в формулу (208), получим
в(1-Д) l-fr
(210)
Р Величину среднего напряжения кручения Хт можно получить следующим образом:
а) мощность, передаваемая рессорой:
Механический к. п. д. i] , может быть принят равным 0,8;
б) средний крутящий момент
Ж„ =71620:!; И 1320
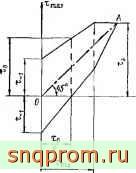
Фиг. 61. Схематизированная дна-грамма Смита.
в) момент сопротивления кручению
г) среднее напряжение кручения
16Af,
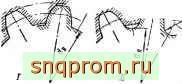
Фиг 62. Конфигурация шлицев рессоры по нормали.
При определении запаса прочности сечения рессоры, проходящего через шлицы, за величину d\ принимаем внутренний диаметр
шлицев,
\ с РЧ расчете на проч
- ность- среднего сечения
рессоры (между шлицами) коэффициент А, равен единице.
При расчете сечения, проходящего через шлицы, величина эффектив иого коэффициента концентрации к-с будет зави сеть от того, как осуществлен переход от боковой поверхности шлицев к впадине. На фиг. 62 приведены два варианта этого перехода, указанные нормалью.
Для напряженных рессор можно рекомендовать применение радиусного перехода (вариант ), как резко снижающего концентрацию напряжений. В этом случае коэффициент А, может быть принят равным 1,25.
Обычно применяют вариант /, для которого коэффициент еле дует принять равным 2--2,5.
В приведенных ииже формулах принимаем ft, =2.
Коэффициенты е н Д, могут быть взяты на основании эксне риментальных данных, приведенных в работе [И].
Для обычно применяемых размеров рессор можно принять ко эффициснт Е=0,9. Коэффициент А, учитывающий влияние качества поверхности и других технологических факторов может быть при нят равным 0,2.
Подставляя эти значения коэффициентов в формулу (210), получим
0,9(1-
1-ц
-0,2) l-f/-n.
l-f2,B
и для среднего (гладкого) сечения рессоры, где fe, =1, эга формула примет вид
,=.-L--. (213)
1 + 1,4
Входящие в эти формулы величины Гш и Гц определяются фор-нулами (211) и (205), а предел текучести tj по экспериментальным .анным для данной марки стали. Обычно для рессор нримепягогся негнрованные стали с Ts=5500 кГ/см.
Для нулевых колес в приведенной формуле (205) Z- действительное число зубьев. Для положительных колес с принятым сме-. щением в=0,5 в эту формулу надо подставить вместо z число, на единицу больше действительного числа зубьев.
При проведении проверочного расчета указанным методом за пас прочности /г, должен быть не ниже 1,3-1,5. Определяем прочность шлицевого соединения Обозначим: zf - число шлицев; т' - модуль;
а'-угол зацепления исходного контура; da - диаметр делительной окружности; 5 dc - наружный диаметр шлицев; dt - внутренний диаметр шлицев; Ь' - рабочая длина шлицев;
а) окружное усилие, передаваемое рессорой:
Р..р=\ (214)
б) напряжише смятия на поверхности шлицев
окр
Примечание. Учитывая неточность изготовления и неравномерность распределения нагрузки между отдельными шлицами, считаем, что нагрузку воспринимают 0,5 всех шлицев.
Допускаемое напряжение смятия для шлицевых соединений при материале с Ов>5000 кПсм рекомендуется ;?й= 1000-1400 кГ/см.
Производим подсчет угла закручивания рессоры.
Определяем угол закручивания для каждого участка рессоры по формуле
<р=- в рм1, (215)
где Ж„ -момент, скручивающий рессору, в кГ-см; L - длина скручиваемого участка рессоры в см; Jp -полярный момент инерции сечения в см*;
п* 163
0..=--модуль упругости второго рода в кГ/см;
£ -модуль упругости первого рода в !{Г1см
ц - коэффициент Пуассона;
G=8-10 кГ/смК
Просуммировав углы закручивания для каждого участка, получим полный угол закручивания для всей рессоры.
Расчет корпуса
Расчет корпуса насоса сводится к опредсчению сечений каналов на линиях всасывания и нагнетания и к расчету на прочность стенок корпуса.
Если к насосу предъявляется требование о возможности реверсивной работы, то камеры нагнетании и всасывания должны быть конструктивно одинаковыми.
При отсутствии такого требования камера всасывания по условиям улучшения заполнения впадин делается значительно птире, чем окно нагнетания.
На фиг. 63 размер окна нагнетания определяется углом Р2. Вьтоднс-ние этого окна в виде узкой щели шириной bi делается с целью уменьшения нагрузки на опоры. С этой же целью иногда делают эту щель несимметричной, смещенной в сторону менее нагруженной ведущей шестерни.
Угод Рь определяющий размеры камеры всасывания, принимается в пределах 45-90°. По условиям улучшения входа и обеспечения бескавитационной работы следует стремитьсм к верхнему пределу значения Pi. Однако для шестерен с малым числом зубьев и высоким давлением нагнетания угол Pi=90 может оказаться слишком большим с точки зрения размеров уплотняюн;ей дуги. В случае применения разгрузки опор от радиальных усилий по схеме, указанной на фиг. S3 верхний предел yr.iia Pi тем более неприемлем, так как он приведет к большим утечкам и резкому уменьшению объемного к. п. д.
Площади сечений окон всасывания и нагнетания выбираются из условий пепревышения допустимых скоростей течения жидкости, которые можно считать следующими:
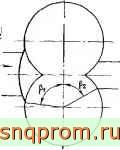
Фиг 6J. Конфигурация окон камер всасывания и нагнета
для обычных насосов без подкачки
иа всасывании f<2 м/сек, а на нагнетании t)<6 м/сек.
Напряжения в стенках корпуса имеют максимальное значение на внутренней поверхности и могут быть определены по формуле Ляме
=P..n,f- (216)
где Dj, - наружный диаметр корпуса;
De - наружный диаметр шестерен или диаметр расточки кор пуса;
Риагн - максимальное давление нагпетания, на которое производится статическое испытание корпуса и которое превышает рабочее давление нагнетания в 1,5--2 раза. Для алюминиевого литья полученное значение о не должно пре-: вышать 5С0 кГ/см и для чугунного литья 700 кГ/см.
При наличии втулок, запрессованных в корпус, необходимо про-; верить расчетным путем напряжения от запрессовки, возникающие в корпусе и во втулке.
На основании задачи Ляме удельное давление, возникающее на поверхности контакта после запрессовки, выражается следующим образом:
, , (217)
где fi - максимальный диаметральный натяг в мм;
d--номинальный диаметр сопрягаемых поверхностей в мм; El £2 - - модули упругости втулки и корпуса в кГ/мм; Ci, Cj - коэффициенты, выражаемые формулами:
d, - внутренний диаметр втулки, ь р.2 - коэффициенты Пуассона материала втулки и корпуса. Найдя таким путем давление р, определяем вызываемое им иа-! пряжение в корпусе по ранее приведенной формуле (216). Иапря-[жение во втулке имеет максимальное значение на внутренней поверхности и определяется по формуле
в конструкциях корпусов насосов, где прямая пересечения расточек не притуплена, возникает концентрация напряжений в точке пересечения этой прямой с днищем колодца. Для уменынения этих напряжений и устранения возможности возникновения трещин в jTofl зоне при высоких давлениях следует снять ребро в месте подхода его к днищу па небольшой высоте
Расчет цапфы ведомой шестерии
Определяем прочность цапфы в сечении d-d (см фиг. 41).
a) изгибающий момент в сечении d-d
б) момент сопротивления изгибу в сечении d-d
b) напряжение изгиба в сечении d-d
r) запас прочности n, найдем из расчета цапфы на усталость.
Цапфа шестерни подвержена знакопеременной нагрузке прн симметричном цикле колебании напряжений.
При этом считаем, что цапфа подвергается изгибу постоянно действующим средним изгибающим моментом.
Для симметричного цикла запас прочности определяется по формуле
(219)
где - эффективный коэффициент концентрации иапряжепип изгиба.
В нашем случае надо взять величину А в зависимости от отношения радиуса галтели к диаметру цапфы.
Это отношение берется равным примерно 0,03. Для этого отношения эффективный коэффициент концентрации =2.4.
Наиболее часто диаметры цапф находятся в пределах 20- -35 ии; дли них средняя величина масштабного фактора Еда=0,8 Следовательно-
(220)

где Ов выражено в кГ1см 166
1 ...
13 14 15 [
16 ]
17 18 19 ...
24