Точная обработка на станке
ИДЕАЛЬНОЕ ЗЕРКАЛО ПОВЕРХНОСТИ — УСЛОВИЕ, ПРЕДЪЯВЛЯЕМОЕ К ШТОКАМ И КОРПУСАМ ГИДРОЦИЛИНДРОВ. ОБРАБОТКУ ИХ ПОРУЧАЮТ ДЕЛИКАТНЫМ, КАПРИЗНЫМ, ОГРОМНЫМ, ДРАГОЦЕННЫМ ФИРМЕННЫМ СТАНКАМ.
ЗАБУДЬТЕ ОЬ ЭТОМ, ПОРАЗИТЕЛЬНО ПРОСТОЕ И ИЗЯЩНОЕ ИНЖЕНЕРНОЕ РЕШЕНИЕ, НАЙДШНОЕ СОВЕТСКИМИ СПЕЦИАЛИСТАМИ, ДЕЛАЕТ ВОЗМОЖНЫМ НАВОДИТЬ «ЗЕРКАЛО» С ПОМОЩЬЮ ЛЮБОГО ТОКАРНОГО СТАНКА, КОТОРЫЙ ЕСТЬ В ВАШЕМ РАСПОРЯЖЕНИИ - ИСТИННО ИЗОБРЕТАТЕЛЬСКАЯ НАХОДКА, ИСТИННО ИЗОБРЕТАТЕЛЬСКИЙ ЭФФЕКТ!
Решительный шаг
Для вас конечно, не составит труда выточить деталь на токарном станке. А вот и станок. Неважно, что Он далеко не первой молодости. Предлагаю вам обработать на нем полость гидроцилиндра длиной, ну, скажем, метров шесть и диаметром 100 мм. С какой точностью? Как того требует деталь, то есть до 40 мкм по диаметру, а шероховатость внутренней поверхности не должна превышать одного микрометра. То же проделать с валом подобных размеров.
Слышу ответ: «Любой токарь знает, что точность обработки подобных деталей на таком станке не превышает десятых долей миллиметра».
Задание уточняю обработка при указанных выше требованиях к точности и чистоте должна длиться пять минут, а установка летали на станке — двадцать
Тут знающий человек только рукой махнет Ему ведом опыт зарубежных фирм. Там такую обработку делают на соответствующем оборудовании, и длится операция часами. Сначала глубокое сверление на специальном высокоточном станке. Время сверления — час. Потом расточка и обработка абразивными мелкозернистыми брусками (хонингование). Бруски вращаются и одновременно совершают возвратно поступательное движение Обработка эта длится еще 2-—3 часа. Но и после нее шероховатость составит 2- 5 мкм — вдвое больше, чем задал автор. Миг пион долларов— такова цене комплекта. состоящего из специальных станков для сверления.
глубокой расточки и хонингования, поставляемых западногерманскими фирмами. При этом станок для хонингования крупногабаритных труб имеет высоту двухэтажного дома над уровнем пола и шахту глубиной шесть метров.
Чтобы больше читателя не интриговать, скажу детали подобные тем, которые я предлагал обработать на токарном станке с упомянутой точностью именно так и обрабатывают на ряде заводов Министерства тракторной и сельскохозяйственной промышленности. Миллионами штук. На обычных токарных станках.
..Началось все несколько лет назад. Рано утром позвонил мне домой из Мелитополя Анатолий Борисович Савелов, заместитель директора (ныне директор) крупнейшего завода в СССР, производящего гидравлику.
—Нет штоков — завод на грани остановки!
Поясню: гидроцилиндры для выносных систем тракторов и сельскохозяйственных машин комплектуют штоками примерно полуметровой длины. Работают они в папе с резиновыми уплотнениями; чтобы уплотнения не изнашивались чрезмерно, штоки обрабатывают, как мы уже говорили, с точностью 40 мкм, а высота шероховатостей на деталях не должна превышать 1 мкм. Этим обеспечивается хорошее уплотнение и надежность работы гидроцилиндров.
На мелитопольском заводе обрабатывают штоки на бесцентрово-шлифовальных станках связанных транспортером в автоматические линии. Работали линии не одни год. в тс и смены, изрядно поизносились Возникли трудности при их ремонте Непросто стало получать абразивные круги нужных марок и размеров Начались поломки простои. И вот звонок замдиректора А мы, словно в ожидании звонка Савелова, уже несколько лет занимались этой волнующей проблемой.
Через три дня со старшим инженером Б Акимовым выезжаем в Мелитополь с неким приспособлением
Комбинированная» головка установлена на обычном токарном станке Решили вместо абразивной обработки применить точение и выглаживание поверхности деталей роликами на обычном токарном станке Оба процесса идут в небольшой, примерно 250x250 мм головке, которую можно ставить на любой токарный станок
Опробовали. Без преувеличения скажу — результаты ошеломили заводчан. Один такой станок с нашим приспособлением превзошёл по производительности и точности традиционные абразивные методы в 2—1 разе. Руководство завода тут же решило внедрять. Но многие запротестовали.
— Не пойдет. При транспортировке на штоках будут забоины.
— Почему?
— Слишком уж гладкая поверхность, все грехи видны!
Действительно, при абразивной обработке поверхность матовая так что не видно даже тонких трещин. Тут поверхность получалась зеркальной.
— Ну что ж, придется аккуратней транспортировать— применить специальную тару,— возразило начальство.
— Велики режимы резания — резцы стоять не будут
— Подберем износостойкую форму резца и марку твердого сплава—простоят не меньше полсмены.
— Штоки надо хромировать, а на такую гладкую поверхность хром плохо ляжет. Шероховатая нужна.
Вроде бы резонное замечание К тому же после нашей обработки на детали оставалась смазочно-охлаждающая жидкость, ее надо как-то снять.
К счастью, с СОЖ все уладилось. Дело в том, что хромированию обычно предшествует электрическая полировка: ток при этом периодически меняет направление, и СОЖ стряхивалась с детали Оказалось к тому же. что применение эмульсии и отсутствие абразивных частиц облегчили предварительную обработку под хромирование Проверили, как после комбинированной обработки (точения и выглаживания) ложится хром на деталь Оказалось, лучше, чем на полированную, потому что теперь на детали нет острых вершин, они прикатывались роликами. Раньше хром оседал на вершинах и чистота поверхности снижалась на целый класс Приходилось драить штоки вручную полировальной шкуркой Это тяж кий труд , Новая технология избавила от него. Теперь после нашей обработки стабильно получали чистоту поверхности на класс выше, чем раньше. Твердость же повысилась в полтора раза, и забоин просто не стало.
Внедрили технологию меньше чем за три месяца. И все же противники не сдавались, мешали осваивать новую технику. Тогда дирекция предприняла решительный шаг: все линии абразивной обработки убрали, а вместо них смонтировали универсальные токарные станки с комбинированными головками Итогом этого мероприятия было то что если раньше обрабатывали штоки четыре линии станков, каждый с двигателем мощностью 25—35 кВт. то есть общей мощностью примерно 600—700 кВт - теперь каждую пятерку абразивных станков заменил один модернизированный токарный мощностью 7 кВт С механизмом подачи в виде двух гидроцилиндров Коробка скоростей упрощена Вместо 600— 700 суммарная мощность теперь 28 киловатт В двадцать с лишним раз меньше!
Резко улучшились и условия труда. Производительность выросла в шесть раз. Точность стабилизировалась.
Станки зарубежной фирмы для хонингования гидронпневмоцилиндров. Стоимость каждого при .мерно 100 тысяч долларов. Однако это самый не дорогой станок из комелька еще два станка для сверления и глубокой расточки. Пена всего комплекта ми 1-тион долларов. Комплект становится ненужным, если вы намерены не пользовать комбинированную конструкцию НИИ стоимостью 600 рублей
Семьдесят четыре тысячи рублей — таков годовой экономический эффект на этом заводе за счет роста производительности. высвобождения рабочих, снижения стоимости обслуживания станков экономии электроэнергии и инструмента.
Жесткость — в меру необходимости
А теперь перейдем к технической сути решения
Цилиндры гидроприводов, клепаны двигателей внутреннего сгорания, золотники гидросистем, штоки и плунжеры гидроцилиндров, оси, валы пальцы гусеничных траков предприятия тракторного и сельскохозяйственною машиностроения делают сотнями тысяч, миллионами Требования к ним — высокая точность изготовления (10— 30 мкм) и малая шероховатость, то есть высота микронеровностей,— не более микрона. Между тем маленькие неточности в каждом эвене кинематической цепи токарного стачка, суммируясь приводят к общей большой неточности изготовления Ее должно компенсировать обработка абразивная. По производительности она раз в пять превосходит лезвийную То же по точности и чистоте поверхности. Однако даёт выигрыш дорогой ценой абразивы снимают металл мелкой стружкой. Это ведет к тому, что расход энергии, например, при шлифовании в десятки раз выше, чем при Обработке точением. Абразивы крошатся, возникают огромные напряжения на поверхности детали. Темпера-ура в 301-е контакта абразива с деталью достигает 1 ООО—1 500 сама деталь нагревается до 600' Отсюда необратимые структурные изменения: падает поверхностная твердость, теряется прочность. появляется сетка поверхностных трещин, возникают остаточные растягивающие напряжения. К тому же процесс сопровождается так называемым шаржированием — поверхность детали насыщается абразивами. И приходишь к тому, от чего пытаешься уйти,— к шершавой поверхности. Поэтому в самых ответственных областях машиностроения например в авиации, абразивная обработка штоков гидро центровка категорически запрещена. Вместо «ее поверхности выглаживают алмазным инструментом, Неглубоко, на несколько сотых миллиметра деформируя их роликами и другими способами Некоторые из этих способов конечно дороже абразивного. Как же быть?
Исследования привели нас к выводу: эксплуатационные характеристики современного лезвийного инструмента за последние годы так выросли что он может конкурировать с абразивами Выросла стой-кость резцов из твердых сплавов с различными покрытиями, и если скорость резания равнялась 50 м/мин лет десять назад, то сейчас ома выросла до 300—500 м/мин
Почему же не используют такие отличные резцы для точное финишной обработки? Причина проста - мало иметь отличный резец надо, чтобы сам станок был точным и жестким. А точность эта обходится чрезвычайно дорого: выше упоминалось о станках стоимостью в миллион дол паров, на которых обрабатывают штоки и корпуса гидроцилиндров.
Идея, которая позволила нам найти достойную замену этим уникумам, теперь кажется удивительно простой: надо разъединить два фактора — точность обработки от точности станка Возникла мысль о небольшой обрабатывающей соловке устанавливаемой в станке, который буде служить для нее приводом, и не более того Ведь сделать точным небольшой узел с малым числом деталей куда проще, чем солидный станок с кинематической целью.
В результате была сконструировала и изготовлена малая (250x250 мм), очень жесткая головка. В нем два оппозитно, то есть друг против друга по диаметру, установлены резцы. Такое расположение резцов приводит к тому, что обрабатываемый ваг или цилиндр не прогибается, как бы <но, под давлением резца, ибо это давление взаимно уравновешивается. Значит точность обработки растет. За резцами — ролики выглаживающие поверхность детали после резания Ролики отлично выглаживают деталь: максимальная высота микронеровностей менее 0.04 микрометра. Совмещение в одной головке резания и поверхностно! о пластического деформирования устранило вибрации, присущие обычному резанию, и повысило стойкость резцов поскольку роликовая головка крепко держит обрабатываемый участок детали. И скорость резания при столь точной обработке может достигать 500 м мин. А все потому, что рабочая головка в отличие от самого станка сотому из минимального числа точно изготовленных, высокопрочных звеньев, влияющих на положение оси вращения относительно вершины резца В свою очередь, вся технологическая система нечувствительна к колебаниям оси вращения детали относительно резцов Сам механизм рабочей головки вращается от узла главного привода станка и перемещается по его же направляющим посредством механизмов и узла подачи станка.
Влияние жестокости приводных узлов станка на точность обработки ослаблено введением демпфирующих звеньев Звенья же дают радиальную жесткость технологической системе на всей длине обработки детали, будь она длиной 500 мм или 20 м! Крепится заготовка в станке с помощью| гидроцилиндра, а гидравлическая система п одерживает постоянное осевое усилие прижима детали
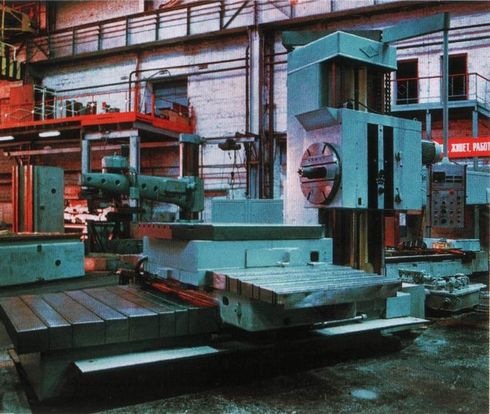
Диапазон снимаемы« припусков весьма широк — от 0,05 до 20 мм. Это позволяет использовать в качестве заготовок горячекатаный и холоднотянутый прокат, литье.
Рабочая головка состоит из последовательно расположенных узлов-модулей для черновой, чистовой и выгораживающей обработки. В качестве деформирующих элементов используют стандартные конические ролики На замену блоков требуется не более 30 секунд!
Стоимость головки примерно 600 рублей.
Признание и вознаграждение — вещи разные
Новая технология получила и международное признание. Бот как это произошло
На предприятиях одной из фирм одевают гидроцилиндры длиной 6—10 м для затворов плотин, шлюзов, судовых механизмов. 3aготовки штоков для цилиндров фирма покупала в ФРГ платя за это золотом Работники фирмы решили делать их сами по традиционной -ихнологии. Вначале обрабатывала одну половину штока поддерживаемого люнетов, заем переворачивали его и обрабатывали другую половину. Далее шлифовали вал на бесцентровых абразивных станках .Одна лишь шлифовка после точения длилась почти 5 часов'
Фирма обратилась в наш институт за помощью.
Спроектировали мы головку для обработки штоков установили ее на суппорт токарного станка. За три прохода головки производится черновая, noлучистовая и чистовая обработка штока Причем за 40 минут снимается слой металла 9 мм на длине пять метров Трудоемкость изготовления штоков уменьшилась в 5 раз!
История эта, однако имела продолжение.
Представители известной западногерманской фирмы, которая поставляет станки для производства гидроцилиндров во многие страны мире получили на Лейп4Игской ярмарке информацию от специалистов ГДР о наших разработках. Фирма обратилась в Министерства станковой промышленности СССР с просьбой ознакомить с технологией, созданной в НИИ тракторной и сельскохозяйственной промышленности .. И вот в институт приехал из ФРГ технический директор фирмы конструктор и-технолог Наступил момент демонстрации устройства. Взяли мы горячекатаную неободранную заготовку диаметром 30 и длиной 700 мм. Представитель фирмы замерил диаметр заготовки засек время Включили станок И с одною прохода за 30 секунд получили готовый практически полированным вал! Ибо шлифовкой такую зеркальную поверхность получить невозможно, обычно деталь еще полируют графитовыми или лепестковыми абразивным кругами
На скорости вращения шпинделя t 200 об мин за проход сняли припуск 2,5 мм на диаметре Точность обработки составила сотую миллиметра, а шероховатость один микрометр. Впечатление было оглушительным: ведь обычно на такую обработку нужно времени в 15 раз больше и минимум три станка: токарный. шлифовальный, полировальный.
Новый метод обработки внедрен на шести заводах Минтракторсельхозмаша. а также в ГДР и Болгарии.
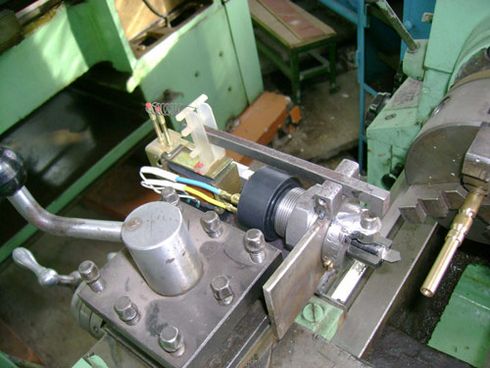
Экономический эффект здесь составляет 80 тысяч рублей в год. Заводской слесарь получил за освоение новшества премию — автомобиль «Москвич» К слову, нам авторское вознаграждение не выплачено ни по одному заводу, хотя со дня внедрения пять лет прошло.
Наш институт — пока единственная организация в стране, сумевшая так улучшить способ комбинированной обработки, что он уже сейчас получил широчайшее распространение в отрасли. Все штоки гидроцилиндров, их полости и гильзы обрабатывают здесь с высочайшей точностью на токарных станках вне зависимости от точности самих станков. На способ оформлено шесть авторских свидетельств и четыре патента (Великобритании США ФРГ Франции). Мы разработали также системы активною контроля размеров обрабатываемой детали с автоматической под настройкой резцов и деформирующих роликов Созданы также специальные автоматы для комбинированной обработки а не только головки устанавливаемые не токарных станках. На сегодня общий годовой экономический эффект составляет почти полмиллиона рублей.
Без сомнения, комбинированная обработка пригодится строительному дорожному, транспортному машиностроению судостроению и ремонту.
Разработчики готовы оказать помощь во внедрении новой технологии.