Главная страница сайта
Российские промышленные издания (узловые агрегаты)
1 ...
5 6 7 [
8 ]
9 10 11 ...
18 Для корригирования зацеПлейия шестерен (роторов) насособ наиболее часто применяется система с коэффициентом коррекции равным 0,5. При этой величине коэффициента коррекции межцентровое расстояние и диаметры роторов (если коэффициент высоты головок f равен единице) представляются стандартными числами, что облегчает расчеты и позволяет применять для контроля нормальный мерительный инструмент.
Расчет межцентрового расстояния и диаметров окружностивысту-пов в этом случае производится по следующим форму,рам:
; - Л^ = /л(2 + 2) = т(2+1) (94)
D, = m(z + 2 + 2g) = m(z + 3). (95)
У роторов, нарезанных с коррекцией \ = 0,5 и смонтированных в корпусе с межцентровым расстоянием = m (z + 1), образуется в зацеплении зубьев боковой зазор С„, величина которого при числе зубьев в пределах от 9 до 22 колеблется соответственно в пределах 0,2 т-0,1 т. В тех случаях, когда желательно достигнуть в зацеплении бокового зазора, отличающегося от приведенных выше величин, а диаметр заготовок и межцентровое расстояние определены по формулам (94) и (95), величина коррекции, отвечающая желаемому значению бокового зазора С„, определяется по следующему уравнению:
Р 2г (шу ск - шу ср) cos ср -
4 sm ср ,
В зарубежной практике производства шестеренных гидронасосов применяются системы корригирования зацепления, отличающиеся от рассмотренных. Например, в насосах, выпускаемых английской фирмой Keelavite, коэффициент кор.рекции рассчитывается по формуле:
g = 0,02 (30 -z).
В насосах, выпускаемых ЕКМ (ГДР), величина коэффициента коррекции роторов с числом зубьев, равным 28 составляет 0,33. В насосах названных фирм применены многозубые роторы, в которых профиль зуба не подрезается. Коррекция при этом позволяет увеличить толщину зуба у корня и за счет этого увеличить прочность зуба. Для насосов, работающих на давлениях 140-160 кПсм, это является весьма важным фактором.
Модуль зацепления и ширина роторов (шестерен)
Когда число зубьев роторов определено, величину модуля зацепления и ширину роторов необходимо определять, исходя из соображений обеспечения заданной производительности насоса. При этом следует исходить из соотношений между величиной модуля и шириной роторов, которые, удовлетворяя заданным габаритам по высоте. Позволяли бы снизить величину нагрузки на роторы и опоры насоса.
6 Рыбкин и Усов 88 . , 81
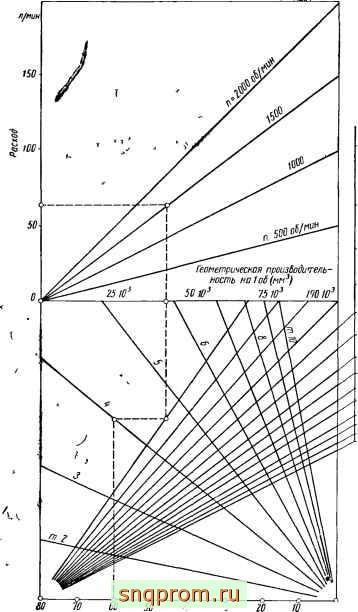
W 30 Ширина роторов
Фиг 36
Расчеты должны основЫва1 сй на известных выражениях для гёб' метрической производительности (6) и для усилия, действующего на роторы (гл III, раздел 2) Величина геометрической производительности насоса пропорциональна произведению квадрата модуля зацепления на ширину шестерен Величина усилия, действующего на роторы, пропорциональна произведению первых степеней величины модуля на ширину роторов Увеличение или уменьшение модуля вызывает, соответственно, сокращение или возрастание нагрузки на роторы, так как для сохранения той же производительности насоса ширина роторов должна быть изменена пропорционально квадрату модуля Например, использование в насосе роторов с модулем, равным 5 вместо 4 позволяет сократить нагрузку на 25%, потому что ширина роторов уменьшится в этом случае в (1,25) = = 1,562 раза
При предварительных расчетах производительности насосов следует пользоваться нижеследующим соотношением между модулем и шириной роторов {Ь = kgtn)
По заданной производительности насоса за один оборот роторов Qг^\) и принятым числу зубьев и величине коэффициента Кв можно определить предварительное значение модуля из уравнения
т
г О)
2лКе(г+21)
При давлении в кГ/см | Коэффициент |
До 10 До 40 Св 40 | До 13 7-9 До 6 |
Значения модуля должны приниматься согласно ОСТ 1597
Для расчета параметров насоса можно также пользоваться номограммой, изображенной на фиг 36 Здесь производительность насоса должна браться с учетом объемного коэффициента полезного действия
Боковой зазор в зацеплении
Известно, что при беззазорном зацеплении в результате двусторонней работы профиля зубьев роторов достигается плавность подачи жидкости (в случае использования избыточного объема отсеченного междузубового пространства) и некоторое увеличение производительности насоса, в отличие от насосов с теми же геометрическими параметрами, но имеющими в зацеплении боковой зазор
Вместе с тем, отсутствие бокового зазора в зацеплении вызывает ряд недостатков в работе насосов При таком зацеплении увеличивается компрессия жидкости в отсеченном междузубовом пространстве и создаются благоприятные условия для заклинивания жидкости даже в том случае, когда коэффициент перекрытия е равен единице Отсеченное междузубовое пространство разделяется на два изолированных пространства, относительное изменение объема которых в процессе беззазорного зацепления больше, чем в процессе зацепления с боковым зазором Это вызывает необходимость предусматривать фрезерование различного рода канавок и скосов или 6* 83
сверление отверстий, соединяющих между собой отсеченные камеры междузубового пространства. Беззазорное зацепление зубьев роторов требует ужесточения допусков на их изготовление и монтаж. При этом опасность заедания зубчатой пары не исключается.
Выбор величины бокового зазора в зацеплении роторов шестеренных насосов должен производиться с учетом специфических особенностей их работы в качестве органов нагнетания и всасывания жидкости. Вопреки этому большая часть рекомендаций по выбору величин бокового зазора в зацеплении зубьев роторов шестеренных насосов основана, главным образом, на условиях работы зубчатой пары в качестве обычной шестеренной передачи. Причиной этого является недостаточное исследование влияния величины бокового зазора на гидравлические качества насосов.
В обычной паре шестерен боковой зазор в зацеплении предусматривается для компенсации суммарных погрешностей в профиле, шаге и винтовой линии зуба (для винтовых зубьев). При этом учитываются также вероятность эксцентричной посадки шестерен на валах, неточное прилегание профилей зубьев, деформации, возникающие под нагрузкой и тепловое расширение. Изготовление зубчатых пар роторов с боковым зазором в зацеплении значительно облегчает технологию производства и сборки шестеренных насосов. При зацеплении роторов с боковым зазором снижается компрессия жидкости в отсеченном междузубовом пространстве и улучшаются условия заполнения междузубовых впадин в зоне всасывания. На основании этого отдельные авторы [29], [12] рекомендуют принимать для роторов шестеренных насосов величину бокового зазора, которая превышает требование обычной зубчатой передачи.
Боковой зазор в зацеплении роторов насосов рекомендуется рассчитывать по соотношению
С„ = (0,08 0,15) т.
Как показывают исследования А. И. Петрусевича [20] и опыты, произведенные в лабораториях (на заводах Красный пролетарий и им. С. Орджоникидзе и в ЭНИМСе), повышенные величины боковых зазоров не оказывают влияния ни на величину динамических нагрузок, вызванных ошибками в окружном шаге, ни на процесс крутильных колебаний, обусловленных ошибками изготовления зубчатых колес.
На шумовую характеристику шестеренного насоса боковой зазор может влиять либо при холостой работе (без давления), либо в случаях, когда величина усилия, прижимающего сопряженные зубья роторов, меньше величины динамической нагрузки, в результате чего возникает поочередное соударение нерабочих профилей зубьев. При этом вредная работа внешней нагрузки (приводной), вызывающей удар, тем меньше, чем меньше боковой зазор. Шум, часто сопровождающий холостую работу насоса или работу при малых давлениях (без кавитации) можно объяснить этими причинами.
Для роторов с винтовыми зубьями корригирование должно производиться с расчетом на минимальный боковой зазор. В некоторых
случаях используется специальное исправление, предусматривающее минимальный зазор в радиальном направлении между цилиндрической поверхностью головок одного ротора и внутренней поверхностью впадин другого. За счет этого можно получить достаточно надежное уплотнение в местах контактирования зубьев и увеличить угол наклона.
Конструктивное оформление и монтаж роторов (шестерен) на валах
Роторы насосов могут изготовляться вместе с валами за одно целое и раздельно от валов. Наибольшее распространение имеет
о =}8°30
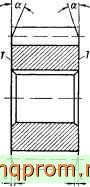
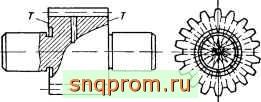
РазВертка поверхности Впадин шестерни
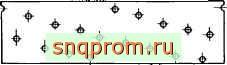
Фиг. 37.
Фиг. 38.
конструктивный вариант со свободной или неподвижной посадкой роторов на валы, изготовленных отдельно от валов. Роторы этого типа конструируются в виде различных модификаций, обусловленных специфическими эксплуатационными или технологическими условиями.
На фиг. 37 изображен рариант конструкции ротора со специальными торцовыми фасками (обозначены пунктиром). Снятием фасок предусматривается образование канала по периферии шестерен с целью некоторого увеличения объема утечек и уменьшения эффекта недозаполнения междузубовых впадин, возникающего вследствие больших окружных скоростей на периферии роторов (до 6 м/сек). В некоторых случаях в роторах производят специальные сверления вдоль оси и (во впадинах и зубьях) перпендикулярно оси (фиг. 38) уравнивания давлений по торцам и разгрузки отсеченного междузубового пространства. Иногда встречаются роторы, изготовленные из двух половин (дисков), каждая из которых смонтирована на валу со смещением по отношению к другой на половину углового шага (фирма Fomag ). Насосы с такими роторами обладают меньшей неравномерностью подачи, что видно на фиг. 39.
Передача крутящего момента производится с помощью шпонок (призматических или сегментных). Способ посадки роторов на валы
путем напрессовки применяется весьма редко и только в насосах низкого давления.
Двусторонние призматические шпонки и шлицевые соединения употребляются в насосах высокого давления с большим крутящим моментом на валу. Применение свободной посадки роторов на валах позволяет торцовым поверхностям занять по отношению к торцам сопряженных деталей определенное положение, соответствующее
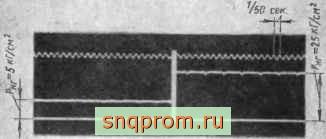
Фиг. 39. Осциллограмма пульсации подачи насоса со сдвинутыми зубьями роторов.
характеру распределения и величине давления в торцовом зазоре. При этом уменьшается опасность задиров на торцах, потому что свободная посадка обеспечивает постоянное сохранение масляной пленки между торцовыми поверхностями. Эту же цель преследует монтаж шестерен на трех шариках. Неподвижная посадка требует
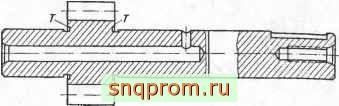
Фиг. 40.
ужесточения допусков на отклонение от перпендикулярности торцов роторов к осям и строгой симметричности расположения шестерен относительно торцов уплотняющих деталей. Несимметричное расположение роторов и перекосы, кроме заедания , ведут к ухудшению объемного к. п. д. Применяются конструкции насосов, у которых вал ведомого ротора является неподвижным. В этом случае в центральное отверстие ротора запрессовывается втулка подшипника скольжения или подшипник качения. Наиболее часто конструкция такого типа применяется во встроенных шестеренных насосах низкого давления, как, например, в радиально-поршневых насосах типа НП завода Гидропривод . Здесь роторы обладают большим числом зубьев 86
(24-28), достаточным для получения торцовой уплотняющей дорожки. Ширина роторов согласуется с шириной выбранных подшипников.
За одно целое с валами роторы (фиг. 40) изготовляются в насосах высокого давления с малым числом зубьев (8-10) большого модуля, когда посадка роторов при помощи паза и шпонки может значительно снизить прочность венца и ослабить вал, несущий большие нагрузки, а также в насосах, где отвод жидкости из отсеченного междузубового пространства осуществляется через специальные отверстия в междузубовых впадинах и валах и при применении специального метода разгрузки шестерен от радиальных усилий (фиг. 38).
Материал, термическая обработка и технические условия на изготовление роторов
Для изготовления роторов насосов применяются главным образом конструкционные стали и реже бронза. В последнее время для изготовления роторов смазочных насосов стали употреблять металло-керамические (железографитовые) материалы Выбор наиболее подходящих материалов для изготовления роторов по техническим и экономическим соображениям при заданных величинах усилия, окружной скорости и характера нагрузки определяется требованиями прочности, и особенно износостойкости, что в значительной мере зависит от характера и степени термообработки.
Основным материалом, из которого чаще всего изготовляются роторы насосов, являются углеродистые и легированные стали. Сталь 45 с закалкой и высоким отпуском (до твердости 250-180) применяются для роторов с окружной скоростью до 1 Jn/ccK при средних величинах удельного давления на рабочую поверхность зубьев. Эта же сталь с нагревом токами высокой частоты и отпуском (до твердости Rc 50-58) применяется для изготовления роторов, к которым предъявляются требования высокой поверхностной твердости зубьев. Сталь 20Х с цементацией и отпуском (до твердости i?c56-62) применяется для роторов с большой окружной скоростью при средних величинах удельного давления на зубья, когда требуется твердая износостойкая поверхность зубьев и вязкая сердцевина. Сталь 40Х с закалкой до твердости Rc 48-50 применяется в тех случаях, когда окончательной обработкой зубьев шестерен является шевингование. При закалке ТВЧ твердость стали 40Х достигается Rc 52 - 54. Для изготовления роторов применяются также стали типа 40ХН, 18ХГТ и 12ХНЗ.
Основной операцией финишной обработки зубьев роторов является шлифование. Шлифованию подвергаются также посадочные и торцовые поверхности роторов. Часто применяется шевингование. Зубья шевингуются до термообработки, после чего шлифуются только торцовые поверхности и наружный диаметр роторов. В этом случае применяется специальная технология закалки, а во избежание искажения рабочих поверхностей зубьев используются специальные
легированные стали типа 12ХНЗА. Роторы насосов должны быть достаточно долговечны, и следовательно, износоустойчивы и высокопрочны. Вместе с этим должен быть строго выдержан класс точности изготовления и обеспечены плавность и бесшумность работы. Первое требование может быть удовлетворено выбором соответствующего материала и его термической обработкой и проверено, в случае надобности, расчетом. Необходимые точность, плавность и бесшумность работы определяются качеством и точностью обработки и сборки зубчатой пары.
В некоторых случаях в качестве финишных операций применяется притирка и парная приработка роторов.
Исследования, проведенные в лабораториях заводов им. Орджоникидзе и Красный Пролетарий , подтверждают, что технология и точность обработки роторов и сборка их в корпусе оказывают значительные влияния на шумовую характеристику их работы. Шевингование корригированными шеверами снижает шум на 12- 15 дб. Поверхностная закалка усиливает шум на 2-3 дб. Перекос осей, не превышающей полуторную допустимую норму и небольшое биение венцов, не оказывают существенного влияния на уровень шума. Развод осей роторов и увеличение бокового зазора в зацеплении не влияет на уровень шума. Уменьшение развода осей риже допустимого ведет к резкому повышению шума. Исходя из этого, применяют, кроме развода осей в корпусных деталях, подрезку зубьев по толщине на 0,05-0,18 модуля больше, чем величина подрезки в обычном зацеплении шестерен. Шум возрастает с увеличением несоответствия профилей и основных шагов зубьев сопряженных колес и при снижении степени чистоты обработки трущихся поверхностей зубьев. Профиль зубьев должен быть плавным (граненность не допускается).
Условия испытания зубчатых роторов на шум должны быть идентичными.
Небольшие изменения в условиях торможения, изменение качеств роторов или жесткости шпинделей шумовой машины могут вызвать заметную разницу в величине шума для одних и тех же испытуемых роторов.
На величину шума влияет конструкция роторов и корпусов, а также монтажные погрешности.
Допускаемая величина шума роторов не должна превышать 82-85 дб.
Предельные отклонения и допуски элементов зубчатых колес, а также предельные отклонения межосевого расстояния назначаются в соответствии с классом точности шестерен в зависимости от диаметра и модуля по нормам, установленным ГОСТ 1643-56 для цилиндрических колес. Этот ГОСТ содержит также нормы на контакт (пятно касания) поверхностей сопряженных колес. Точность изготовления шестерен (роторов) насосов низкого давления по всем параметрам зацепления принимается обычно по III классу, а насосов среднего и высокого давления по II и I классу. Класс точности изготорденич указывается на рабочем чертеже. Кроме 88 .
того, на рабочем чертеже должны быть указаны: число зубьев, модуль (для винтовых зубьев нормальный /л„ и торцовый модули), угол профиля исходного контура, угол наклона винтовых зубьев, коэффициент коррекции и размеры для проверки толщины зуба путем измерения по постоянной хорде, или по общей нормали, в зависимости от принятого на заводе метода контроля. На рабочем чертеже указываются также допустимые величины отклонений от правильности геометрических форм и взаимного расположения поверхностей шестерен. Эксцентричность расположения начальной окружности и окружности головок не должна быть выше 0,02-0,03 мм. Допустимая разность ширин роторов (непараллельность торцов) не должна превышать 0,005-0,01 мм. Неперпендикулярность торцовых поверхностей к осям роторов должна быть в пределах 0,01-0,02 мм на расстоянии в радиальном направлении, равном 50 мм. Конусность и овальность роторов по наружному диаметру
f , J Таблица 3
Формулы для расчета параметров прямозубого зацепления
Параметры
Формулы для расчета величины параметра
Межцентровое расстояние
Угол зацепления
Ск = arccos
= arccos
{Ac s .) =
z+21
cos co
Диаметр окружности головок
De = {z + 2 + 2l)m
Угол давления в точке профиля на окружности головок
ае = arccos cos
Толщина зуба по окружности головок
Se = De (- + -y-tg ао + inv оо - inv а^
Толщина зуба по делительной окружности
Высота головки до хорды делительной окружности
De - mz cos (~ + -у- tg
Толщина.зуба по постоянной хорде
Sn.x = m(~ cos со + gsin 2ао
Высота головки зуба по постоянной окружности выступов
hn.x = h - m sin 2ао + I sin а^
Длина общей нормали
L= т cos ctd [я (rt-0,5) + 2g tg ао4- inv a],
где rt - число охватываемых при измерении зубьев
не должна быть более 0,01 мм, В большинстве случаев техническими условиями предусматривается получение острой кромки между цилиндрической поверхностью головок и торцами шестерен, во избежание появления дополнительного пути утечек жидкости. Однако, как сказано ранее, имеют место отступления от этого правила (фиг. 37). Отклонение от соосности поверхности посадочного отверстия и наружного диаметра зубчатого венца не должно превышать 0,015-0,02 мм.
При изготовлении роторов заодно целое с валами на рабочем чертеже должна быть обозначена допустимая соосность опорных шеек с наружным диаметром зубчатого венца, которая не должна превышать 0,01-0,015 мм. На чертеже ведущего ротора вала указывается также отклонение от соосности опорных шеек и поверхности приводного конца вала. Допустимое отклонение не должно превышать 0,015-0,02 мм.
Расчетные зависимости, необходимые при конструировании j и контроле прямозубых роторов с корригированным профилем, помещены в табл. 3.
Указания по расчету на прочность
Для насосов с рабочим давлением, не превышающим 40-50 кГ/см, рассмотренные и установленные ранее значения модуля удовлетворяют прочностным требованиям с достаточным запасом. (Величина модуля установлена, исходя из заданной производительности и минимальных габаритов насосов.) При конструировании насосов для j давлений, превышающих 50 кГ/см, рекомендуется производить проверку соответствия принятых значений параметров зацепления условиям работы насоса. Расчет рабочих поверхностей зубьев на долговечность по контактным напряжениям и расчет зубьев на выносливость по напряжениям изгиба следует производить по методу А. И. Петрусевича, подробно изложенному в Энциклопедическом справочнике Машиностроение (т. 2) и Справочнике машиностроителя (т. 4). При определении напряжений изгиба наиболее неблагоприятным следует считать момент выхода из зацепления зуба ведущего ротора. Расчетное окружное усилие определяется в этом случае по формуле
tsae- (tg а --У^
р вд (наиб)
Ом 03 (наиб1 2 103 }/l + (tg а,-)
Потери на трение в зацеплении
При расчете потерь мощности необходимо учитывать потери на трение в зацеплении. Методика расчета подобных потерь подробно разработана проф. Л Н. Решетовым. Потери мощности на трение в зацеплении слагаются из постоянных потерь при отсутствии нагрузки и переменных потерь, пропорциональных нагрузке. 90
1 ...
5 6 7 [
8 ]
9 10 11 ...
18