Главная страница сайта
Российские промышленные издания (узловые агрегаты)
1 ...
11 12 13 [
14 ]
15 16 17 18 втулок и вызвать отжим или перекос торцов втулок. Преимуществом такого способа поджима является относительное равновесие втулок, предохраняющее их от перекоса, и сравнительная простота конструкции.
На фиг. 69 показана другая разновидность системы дифференциального поджима. Прижим плавающих втулок 1 к роторам 2 осуществляется давлением жидкости, подводимой по каналу 3 из камеры нагнетания. Площадь торцов втулок, на которую давит жидкость, изолирована уплотняющими кольцами 4 и 5. Дифферен-
Разрез по lb
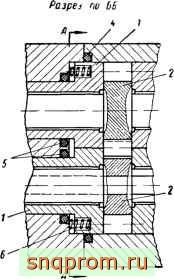
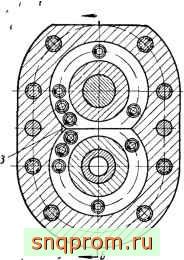
Фиг 69
циация усилия прижима создается цилиндрическими пружинами сжатия 6. На стороне нагнетания количество пружин увеличено. Можно обеспечить достаточно большую точность величины усилий прижима путем подбора пружин и выбора места их размещения. Недостаток этой конструкции состоит в том, что ее применение ограничивается только очень небольшим диапазоном рабочих давлений. Конструкция, изображенная на фиг. 69, является более простой, чем другие конструкции с системой дифференциального поджима.
3) Наиболее правильной по принципу, но наиболее сложной по исполнению является конструкция следящего поджатия уплотняющих втулок, изображенная на фиг. 88. Плавающие втулки 5 прижимаются к шестерням I и 2 поршнями 7, число которых равно числу междузубовых впадин. Жидкость подводится под поршни по каналу 8 от участка торца шестерни, с которым контактирует участок втулки, поджимаемый данным поршнем. Число зубьев каждого ротора равно семи. Пружины II служат для поджима втулок в момент пуска насоса. Насос рассчитан на рабочее давление
до 200 кГ/см. Преимущество указанного способа поджима состоит в возможности обеспечения необходимого усилия прижима во всем диапазоне рабочих давлений, так как величина усилия поджатия каждого из семи поршней представляет собой функцию давления в зоне торцового зазора, ограниченного соответствующей междузубовой впадиной. Недостатком этой конструкции является ее сложность.
Оригинальное конструктивное решение метода следящего (дифференциального) прижима изображено на фиг. 70. Гидравлическая
Разрез по 5£
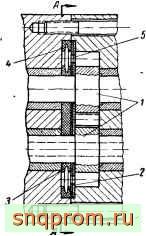
Разрез по М
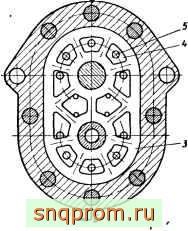
Фиг. 70.
компенсация торцовых зазоров выполняется в этом насосе с помощью гибкой биметаллической (бронза-сталь) уплотняющей пластины 2, прижимаемой к торцам роторов давлением жидкости. Зазоры между пластиной 2 и крышкой уплотняются специальным армированным уплотнением 3, изготовленным из синтетической резины, которое одновременно предохраняет утечку жидкости по валам. Этим же уплотнением поверхность пластины 2, со стороны обратной к роторам, разбивается на ряд камер 4, числом равным числу междузубовых впадин. Каждая камера соединяется с междузубовой впадиной отверстием 5 малого диаметра, сделанным в пластине 2. Давление в каждой камере определяется положением отверстия 5 и является функцией градиента давления внутри междузубовых впадин. Размеры отверстий и их положение тщательно рассчитываются. Эта конструкция насоса более проста, чем конструкция со следящим (дифференциальным) прижимом поршнями (фиг. 88). Затруднение представляет лишь изготовление сравнительно сложного по конфигурации уплотнения.
Применение прямого, дифференциального и следящего методов поджима плавающих втулок или мембран приводит к уменьшению
торцовых зазоров, что, в свою очередь, уменьшает утечки и увеличивает объемный к. п. д. шестеренных насосов, работающих при больших рабочих давлениях (свыше 70 кГ/см).
Вместе с тем применение гидравлической компенсации торцовых зазоров влечет за собой значительное усложнение конструкции шестеренных насосов. При этом возникает необходимость использования дефицитных дорогих антифрикционных материалов (оло-вянистая бронза, баббиты, легированные алюминиевые сплавы и др.).
Гидравлическая компенсация торцовых зазоров снижает механический к. п. д. шестеренных насосов и повышает в связи с этим потери мощности.
Необходимость проведения длительных экспериментальных, расчетных и конструкторских работ для определения оптимальных усилий поджима и места их приложения увеличивает трудности применения гидравлической компенсации торцовых зазоров.
Это привело к поискам и созданию иных конструктивных решений, используемых (для гидравлической компенсации зазоров) в шестеренных насосах повышенных давлений (70-160 кГ/см) и обеспечивающих достаточно высокие значения объемного к. п. д. Широко применяется, например, принцип сочетания больших размеров уплотняющих торцовых поверхностей (роторов с большим числом зубьев) с точно гарантированными размерами торцовых зазоров, получаемых в результате строгой осевой фиксации валов и шестерен (роторов) по отношению к корпусу. (Конструкции таких и других насосов рассматриваются в следующей специальной главе настоящей книги).
Единой методики выбора величины площади поджатия и определения усилия прижима до настоящего времени не создано. Это объясняется сложностью гидродинамической задачи, при решении которой устанавливаются закономерности распределения давления в торцовом зазоре работающего насоса. Затруднения возникают из-за того, что необходимо учитывать непостоянство величины торцового зазора, вызываемое многочисленными причинами: биением торцов роторов; различием диаметров тел качения подшипников (в случае применения подшипников качения); пульсацией давления в нагнетательной магистрали; компрессией жидкости в междузубовых впадинах; неровностями на поверхности торцов роторов и уплотняющих деталей; неплоскостностью соприкасающихся поверхностей роторов и уплотняющих деталей; упругой деформацией поверхностей скольжения зубьев в зонах контактирования; действием неуравновешенных масс привода.
Учесть с необходимой точностью степень влияния каждой из перечисленных причин и установить закономерности изменения торцового зазора как функции их совокупного действия является задачей большой сложности. Поэтому все известные методы расчета неизбежно включают ряд допущений, делающих их приближенными.
А. Ф. Осиновым [16] дано в общем виде решение известного уравнения движения капельной жидкости:
Vy - grad р = е (wV) V; div (у) = О,
которое выведено для случая течения жидкости в зазоре между двумя круглыми пластинами, одна из которых скользит с угловой скоростью О), а зазор между ними изменяется со скоростью V. Решение этого уравнения получено при следующих допущениях. Характер изменения скорости V принимался синусоидальным
а функция рассматривалась лишь в первой четверти периода 0 < а < . В остальных /4 периода - < а < tj скорость
изменения торцового зазора v считалась равной нулю
Учитывалось лишь радиальное течение жидкости со скоростью (Составляющая скорости считалась пренебрежимо малой по сравнению с у^)Член отбрасывался, как много меньший члена
Составляющая скорости рассматривалась лишь как функция параметров гиг.
С учетом перечисленных допущений общее дифференциальное уравнение движения в цилиндрических координатах запишется
в следующей форме:
дг) дг~ г д , , , dv,
(130) (131) (132)
Обозначив изменяющуюся величину торцового зазора через б„ и считая давление в зазоре лишь функцией радиуса [р = р (г)], найдем решение этого уравнения, используя следующие граничные условия: I J
! z= 0; v, = 0; = 0; v = 0;
z = 8 , y, = 0, v,= ~v, y = (ur;
г = ri, p = 0; 1 ,
z = r; p = p ,; j
Подстановкой граничных условий в выражения, полученные после интегрирования уравнений (130) и (131), определяют значения функций V, и vr:
\ dp , с, ч , <uV г<\
rbl dp
Используя значения и Vr и соответствующие граничные 144
условия, после интегрирования получим уравнение для определения давления в торцовом зазоре, на внешней границе которого = р„/.
p = 3f. (г
Здесь
20v Б'
.(133)
Ti - радиус внутренней границы торцового зазора; г2 - переменный радиус с пределами изменения от Rg до R, который В большинстве случаев для упрощения принимается равным Ri. Формула (133) может быть использована для определения значений давления в точках торцового зазора уплотняющей зоны. Для этого необходимо вместо давления подставить переменное давление pj в соответствующей междузубовой впадине, находящейся в уплотняющей зоне. Характер изменения давления р, установлен при рассмотрении объемных потерь и нагрузки на шестерни и опоры.
Зависимость (133) для давления р в торцовом зазоре обязывает сделать вывод о правильности лишь такого конструктивного решения гидравлической компенсации торцовых зазоров, в котором усилие прижима в каждой из точек поджатия уплотняющей детали будет являться функцией давления в соответствующей точке на периферии роторов, т. е. система гидравлической компенсации торцовых зазоров должна быть следящей . Необходимые соотношения между
площадями поджатия F
И скольжения F могут быть найдены
из уравнения равновесия подвижной уплотняющей детали
Re (Риг^подж
РнгРвпнг +
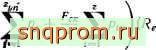
где
G p - усилие пружины;
- число междузубовых впадин, находящихся в зоне нагнетания,
Zy - число междузубовых впадин, находящихся в уплотняющей зоне насоса;
Zee - ЧИСЛО междузубовых впадин, находящихся в камере всасывания,
X - величина смещения точки приложения уравновешивающего усилия.
Для герметичности торцового зазора необходимо, чтобы
>
/=1 / =1 J
В этой зависимости площадь скольжения представляет собой сумму площадей торцов зубьев zF и площади торцового кольца, ограниченного окружностями впадин и диаметром вала, т. е.
10 Рыбкин и Усов 88 л 145
в приведенных выше расчетных зависимостях содержится большое число параметров, величины которых могут быть определены лишь экспериментально, что является основным недостатком этого метода расчета и затрудняет его практическое использование.
Еще больш! е допущения содержит методика расчета площади поджатия, предлагаемая Е. М. Юдиным [27]. В этом методе игнорируется непостоянство величины торцового зазора и существование
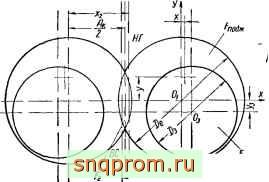
Фиг. 71.
градиента давления в зазоре между торцовой площадкой зуба и сопряженной торцовой поверхностью уплотняющей детали при изменении радиуса от до R.
Е. М. Юдиным предлагается следующая формула для вычисления площади поджатия:
где ij) - центральный угол, соответствующий размерам камеры нагнетания (фиг. 71); Фо - центральный угол, соответствующий размерам камеры всасывания.
Координаты центра тяжести площади поджатия можно определить из равенства моментов гидравлических сил, возникающих от действия полного давления на площади Рподж моментов сил, действующих со стороны роторов.
После упрощений и приближений получены следующие значения координат центра тяжести площади Fq:
17.3 [Rl - R) 4- 5.3 [3i?f- [rl + 4r, + r,]]
20 [3Rl-{R, + R,r,rl)\
0.7 {Rl -R)+ 5,3 \3R] - {4 + rlR, + rf)
SRl~{R,+R,r + 4)
Конструктивно изоляция площади поджатия от зоны всасывания может быть осуществлена с помощью специальных резиновых колец, выделяющих на торцаХ уплотняющих деталей круговые площади по диаметру D. Координаты центра круга {х^, у^) диаметром /)з могут быть найдены из условий нулевого значения статических моментов плоских фигур относительно осей, проходящих через их центр тяжести ,
. Рподж .
Уз - У р-
= е - i в[2агс COS - sin (2arc cos
Dg sin ( 2arc cos
A I A \
2arc cos - sm ( 2arc cos
Рекомендуемое E. M. Юдиным смещение центра изолированной круговой площади вправо от оси у (с положительным значением координаты JCg) является необоснованным, так как в этом случае возникает опасность перекоса торцов уплотняющих подвижных втулок вследствие того, что жидкость под давлением нагнетания будет давить на большой участок их торцовой поверхности, примыкающей непосредственно к зоне всасывания. Более целесообразно смещение центра Од влево на столько, чтобы в результате
X,- . п .
В насосах фирмы Plessey , хорошо зарекомендовавших себя при эксплуатации, участок торцовой поверхности втулок, сопряженный с зоной всасывания, полностью изолируется (фиг. 90). Площадь поджатия для одной уплотняющей втулки этого насоса составляет примерно 8,95 см. Расчет же площади поджатия по формуле (135) дает величину 6,02 сж, которая может оказаться недостаточной. Такие расхождения между теоретическими и практическими значениями площади поджатия являются следствием упомянутых выше допущений, положенных в основу выводов расчетной зависимости для Р„одж-
Экспериментальные данные [16] показывают, что конструкции насосов с прямым и дифференциальным поджимом торцовых втулок удовлетворительно работают до давлений, определяемых неравен- 1200
СТВОМ Р„е(наиф<ОА-
to* 147
в насосах, рассчитанных на более высокие давления, должна быть применена следящая система поджатия.
Для первых двух способов поджатия удельное давление на кон-тактирующихся поверхностях определяется зависимостью
Я~-р-Риг и-пи Я--р---,;:об5 *
Тел fCK D
е
Опытное значение q au(), ри котором сохраняется устойчивая работа насоса, соответствует отношению = 1,35. Тогда
lfTO
Яиаиб j~p еъ
Для конструкций насосов со следящей системой прижима, когда удельное давление определяется по формуле
Рповж - Рвп
Гек и -
наибольшее удельное давление составит: *
10. УПЛОТНЕНИЯ ПРИВОДНОГО ВАЛА И СВЯЗАННЫЕ С НИМИ ПОТЕРИ
Уплотнения приводного вала в шестеренных насосах преследуют следующие цели: а) предотвращение засасывания воздуха в камеру всасывания; б) предотвращение утечек рабочей жидкости наружу, в) предохранение от попадания посторонних частиц внутрь насоса.
В современных шестеренных насосах в основном применяются три типа уплотнений: а) мягкие набивные без автоматической компенсации износа; б) манжетные с автоматической гидравлической или механической компенсацией износа; в) торцовые с автоматической компенсацией износа механическим или гидравлическим способом.
Как правило, в шестеренных насосах в зоне уплотнения уплотняемая среда (масло) имеет избыточное давление до 2 кПсм.
Мягкие набивные уплотнения (фиг. 72, а) применяются, в основном, в насосах низкого давления. Компенсация износа в мягких уплотнениях происходит за счет затяжки винтов прижимного фланца. Вслед за уплотнением обычно располагается камера 1, из которой отводятся утечки. Коэффициент трения мягкого уплотнения зависит от материала набивки, степени затяжки фланца, чистоты обработки вала и, в меньшей степени, скорости вращения вала
Для хлопчатобумажной набивки коэффициент трения р, находится в пределах 0,06-0,11, а для асбестовой набивки в пределах 0,03- 0,07. Скорости скольжения (окружные скорости) допускаются до 4-5 м/сек. Давление на уплотнение не должно превышать 0,15-
0,2 кПсм. Можно применять для набивки пробковый материал, причем натяг пробкового кольца по диаметру выбирается примерно равным 1 мм (для валов диаметрами до 30 мм).
Мягкие набивные уплотнения не создают условий герметичности, и утечки по валу составляют (на масле марки Индустриальное 20 ) примерно 0,3 см/мин на 1 см длины окружности
Момент трения уплотнений вращательного движения рассчитывается по формуле
М^. = к^Р, кГ/см, (136)
где d - диаметр вала в см; Fyn=mil - площадь поверхности уплотнения в см; I - длина уплотнения в см;
k - напряжение силы трения (удельное трение в кПсм). Для пробковых мягких уплотнений после 2 час. приработки с последующей подтяжкой прижимного фланца k = 0,006 кГ/см.
Наиболее часто в шестеренных насосах применяют манжетные уплотнения, изготовленные из маслостойкой резины (фиг. 72 б). Расположение уплотнения в крышке насоса упрощает его монтаж. Для обеспечения герметичности по наружному контуру уплотнения натяг по наружному диаметру должен быть в пределах 0,3-0,8 мм. Устранение утечки по поверхности вала достигается за счет небольшого натяга кольца по внутреннему диаметру и за счет натяжения кольцевой пружины 1. Для нормальной работы уплотнения необходима смазка, в результате чего абсолютная герметичность не обеспечивается. Трение в уплотнениях зависит от размеров вала, давления уплотняемой среды, чистоты обработки вала, скорости вращения вала и характера материала уплотнения. Усилие трения на единицу длины уплотняющей кромки кольца из маслостойкой резины марки 3825 по ТУ 1166-51-МХП регламентируется величиной порядка 0,1-0,25 кГ/см. С увеличением давления жидкости трение в уплотнении возрастает, а с увеличением скорости несколько понижается. Установка специального шарикового клапана для создания давления перед уплотнением (в камере 2) в пределах 0,5-0,1 кГ/см позволяет получить надежную работу уплотнений и компенсацию износа за счет разжима уплотняющей кромки давлением.
При монтаже манжетных уплотнений (если позволяет конструкция уплотнения) ширину канавки b (фиг 72, б) делают на 0,5-0,8 мм меньше ширины уплотнительного кольца с тем, чтобы при сборке уплотнений за счет прижима торцов кольца создавалось дополнительное уплотнение В некоторых случаях камеру 2 соединяют с зоной всасывания, хотя это может привести к нежелательному подсосу воздуха по валу насоса Для исключения возможности подсоса воздуха по валу насоса часто применяют конструкцию с двумя манжетными уплотнениями (фиг 72, в) Применение конструкции с двумя уплотнениями, поставленными навстречу одно другому, позволяет устранить утечки жидкости по валу и предотвратить подсос воздуха.
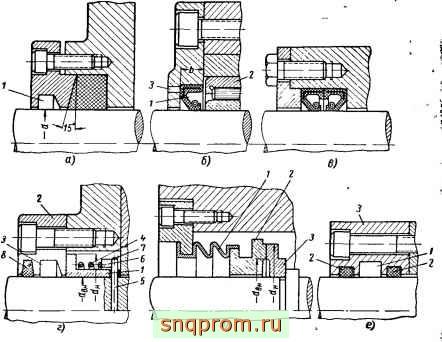
Фиг. 72. Конструкции уплотнений приводного вала.
два-три отверстия 3 (фиг. 72, б). Для манжет из маслостойкой резины напряжение силы трения принимается в пределах 0,07- 0,08кГ/см. (Данныеориентировочные, так как трение зависит от силы нажатия кольцевой пружины, температуры масла, качества поверхности вала, свойств резины и от натяга манжеты на валу.)
Одним из распространенных типов жестких (или так называемых механических) уплотнений вала в шестеренных насосах являются торцовые уплотнения, изображенные на фиг. 72, г.
Уплотнение осуществляется путем контактирования торцовых поверхностей вращающейся с валом втулки 1 и неподвижной крышки 2. Втулка имеет посадку на вал, обеспечивающую продольное перемещение (обычно применяется посадка С). Для предотвращения провертывания втулки относительно вала служит штифт 5, который входит в торцы втулки. Для обеспечения прижима втулки к крышке служит пружина 4 и кольцо 6. Усилие пружины определяется экс-
150 ]
Скорости вращения вала и давления уплотняемой среды, допускаемые при манжетных уплотнительных кольцах, оТ]ределяются наибольшим допустимым нагревом вала и кольца, который вызывается трением уплотнительных колец. При применении манжетных уплотнений необходимо иметь чистоту обработки поверхности вала не менее Н^ = 0,4 мк. Вал в местах контакта с уплотнением подлежит закалке. Для выбивки уплотнений из крышки обычно делаются
1 ...
11 12 13 [
14 ]
15 16 17 18