Главная страница сайта
Российские промышленные издания (узловые агрегаты)
1 ...
10 11 12 [
13 ]
14 15 16 ...
18 Рва S Г/см
Рнг 8 UcM

2 3 и 1 г 3 I* 5
I Фиг 60 Осциллограмма давлений в разгрузочных канавках.
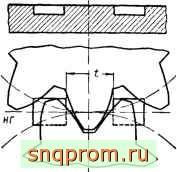
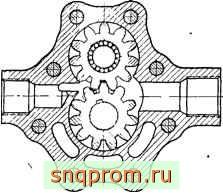
а) 6)
Фиг. 61. Схема расположения разгрузочных канавок.
\ / Сечениеподд
> ВС
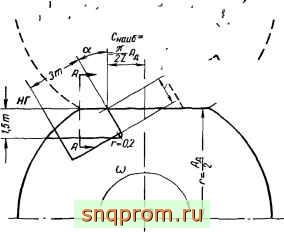
Фиг. 62. Размеры разгрузочных канавок со скосами
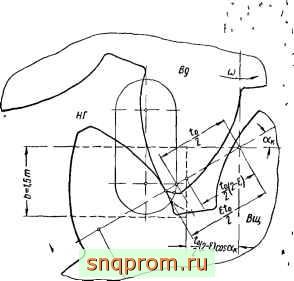
Фиг. 63.
поэтому расчет следует вести по наибольшим значениям скорости изменения объема отсеченного междузубового пространства.
Ранее установлено, что скорость изменения объема отсеченного пространства характеризуется зависимостью
с наибольшим значением д
Яизб (наиб) = 4 сог^Ь (tg а, - tg а;, - ) = шЬ (е - 1).
Таким образом, независимо от способа подвода и отвода жидкости площадь сечения канала должна определяться из соотношения
f 1 изб (наиб) <о(е-l)tofe /126)
где /каи - площадь сечения канала; Яизб (наиб) - наибольшее значение скорости изменения объема отсеченного пространства; кан - скорость движения жидкости в канале в м1сек. В случае выполнения каналов в виде сверлений во впадинах зубьев эта формула позволяет определить диаметр сверления непосредственно. При канализации жидкости посредством торцовых канавок глубину их следует определять с таким расчетом, чтобы наименьшее значение площади проходного сечения в плоскости, перпендикулярной к плоскости чертежа соответствовало величине
Если представить сечение канализационной канавки в форме условного прямоугольника со стороной С, лежащей в зоне зацепления и стороной представляющей глубину канавки, то искомая площадь проходного сечения при движении жидкости в канавке по направлению к зоне нагнетания представится в виде уравнения:
, Chau = (при двух канавках).
Графические расчеты показывают, что С следует принимать, равным примерно 0,45т.
Тогда глубину канавки к^н можно определить из уравнения (для двух канавок):
Полагая = nmcos а = 2,952 т (при применении инструмента с 20° углом профиля), получим следующую формулу для определения глубины канавки:
т(е - \)<йЬ
К
(127)1
Расчет элементов зацепления роторов для устранения явления заклинивания жидкости
Посредством изменения некоторых параметров зацепления можно' полностью устранить возможность возникновения защемления жидкости. Процесс заклинивания жидкости, как известно, происходит на участке линии зацепления АС (фиг. 64) в промежутке вращения от начала одновременного контактирования двух пар зубьев до контакта, соответствующего симметричному расположению точек на линии зацепления С и D. При этом объем отсеченного пространства возрастает до момента выхода из зацепления одной изпарзацепляющихсязубьев.
Если параметры зацепления выбрать так, чтобы одновременное контактирование двух пар зубьев наступало лишь в точке С, то заклинивание жидкости не будет иметь места.
Это может быть осуществлено следующими двумя способами.
Первый способ. Наружный диаметр одного из роторов (на фиг. 64 - верхнего) уменьшается на величину 2Аг с расчетом, чтобы начало контактирования зубьев ведущего и ведомого роторов происходило в точке С, гнев А, как обычно. Для компенсации уменьшения диаметра одного из роторов с целью сохранения геометрической производительности насоса диаметр сопряженного ротора увеличивается на такую же величину. При этих условиях объем отсеченного пространства будет i изменяться только в сторону увеличения. Следует учесть, что насос!
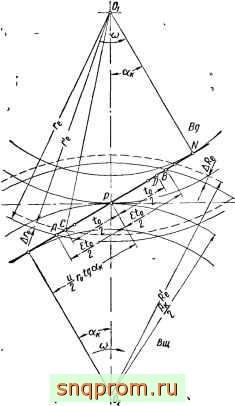
Фиг. 64.
при этом не может быть реверсивным. Если необходимо сохранить возможность реверсирования, то внешние диаметры обоих роторов должны быть уменьшены. При этом, разумеется, сократится производительность насоса.
Изготовление роторов при изложенном способе устранения явления заклинивания производится нормальным 20° зуборезным инструментом. Различие при нарезании ведущего и ведомого роторов состоит лишь в величине положительной коррекции. Расчет величин коэффициентов инструмента и определение геометрических размеров ведущего и ведомого роторов производится на основании элементарных соотношений теории зацепления.
Примем расстояние между осями зацепляющихся роторов
А, = г + 2 = г+1.
Обозначения на фиг. 64 представляют собой:
R - искомый радиус окружности головок ведущего ротора;
/ - радиус окружности головок ведомого ротора; и Rg - радиусы окружностей головок роторов при равных величинах коэффициента коррекции; Аг = - rg-- величина уменьшения радиуса заготовки ведомого ротора и соответственного увеличения ведущего ротора.
Обозначения прочих геометрических параметров зацепления известны из предыдущего. Тогда:
I г.
Определив Ar, найдем, что радиус заготовки ведущего ротора
R, = Re + Аг,.
Существенным недостатком рассмотренного метода устранения возможности защемления жидкости является необходимость изготовления роторов различных диаметров и выполнения в корпусе насоса различных расточек. Более целесообразным следует считать применение роторов равных диаметров с компенсацией связанных с этим потерь производительности, соответствующим увеличением ширины роторов. Аналогичный принцип устранения возможности защемления жидкости заложен в снятии фасок на рабочей стороне зуба ведомого ротора [29]. Снятие фаски по размерам, указанным на фиг. 65, позволяет устранить возможность защемления, так как зубья ведущего и ведомого роторов вступают в контакт только в момент симметричного расположения точек контакта зубьев на линии зацепления.
Следует иметь в виду, что шлифование скосов на рабочих сторо нах зубьев является операцией трудоемкой и дорогостоящей.
Второй способ.
Необходимое условие для устранения возможности заклинивания жидкости, требующее начала контактирования зубьев ведущего и ведомого роторов в тот момент, расположения точек контакта на расстоянии половины основного шага от полюса зацепления, может быть выполнено путем соответствующего увеличения межцентрового расстояния. При этом размеры
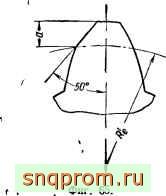
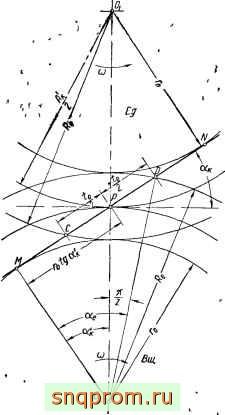
Фиг 66.
роторов должны сохраняться те же, что и при обычных условиях зацепления. Схема такого зацепления изображена на фиг. 66.
Величина межцентрового расстояния А' при этой схеме зацепления может быть определена из следующего соотношения:
(128)
Угол зацепления а' при этом становится равным
8. УПЛОТНЯЮЩИЕ ПЛАСТИНЫ, КРЫШКИ И ВТУЛКИ
Уплотняющие пластины применяются в насосах многослойной компоновки для изоляции рабочих камер и уплотнения торцов роторов. Встречаются следующие их конструктивные разновидности:
1) пластины, выполненные по форме наружных очертаний корпуса, устанавливаемые между торцами корпуса и крышками насоса (фиг. 73, а);
2) пластины, выполненные по форме внутренних расточек корпуса (в виде цифры 8), устанавливаемые внутри корпуса в пространстве между торцами роторов и привалочной плоскостью (фиг. 73, б);
3) утолщенные пластины, в расточках которых размещаются опоры роторов (фиг. 74, 81);
4) утолщенные пластины, выполняющие одновременно функции крышек с расточками под опоры роторов (фиг. 80).
В насосах с прямозубым зацеплением на торцах уплотняющих пластин фрезеруются или рассверливаются разгрузочные канавки.
Уплотняющие пластины изготовляются из антифрикционных чугунов различных марок, бронзы, закаленной стали и алюминиевых сплавов.
Торцовые поверхности пластин (по плоскостям разъема) подвергаются чистовой обработке: шлифованию, тонкому точению, а иногда и притирке. Отклонения от плоскостности стыковых поверхностей допускаются только в сторону вогнутости. Предельное отклонение не должно превышать 0,005 мм. При утолщенных пластинах с расточками под подшипники отклонение от перпендикулярности плоскостей разъема к осям отверстий под подшипники не должно превышать 0,01-0,02 мм на радиусе длиной 50 мм. Допуски на межосевые расстояния определяются классом точности зацепления и колеблются в пределах + 0,02-0,03 мм. В тех случаях, когда расточки в уплотняющих пластинках представляют собой опоры скольжения к качеству поверхности, точности изготовления и материалам предъявляются особые требования.
В насосах пакетной компоновки с центрированием деталей по расточкам корпуса крышки выполняют лишь вспомогательные функции, предотвращая появление наружной течи жидкости (фиг. 76). Аналогичная роль предназначена крышкам в некоторых конструкциях насосов с многослойной компоновкой (фиг. 79-81).
В передней крышке размещается уплотнение приводного вала. В конструкциях, где ведущий вал выводится одновременно в обе стороны, уплотнение размещается также и в задней крышке. Материал крышки обычно тот же, что и материал корпусов (чугун, алюминиевые сплавы). Возможно изготовление крышек из пластических масс.
Основным техническим условием на изготовление крышек является требование соблюдения плоскостности стыковых поверхностей в пределах до 0,005 мм (в сторону вогнутости). В случаях, когда для уплотнения стыков между крышками и корпусом используются кольцеобразные уплотнения, требование в отношении отклонений от плоскостности может быть снижено,
Использование крышек для размещения в них подшипников имеет место лишь в насосах с многослойной компоновкой (фиг. 73, а, б, 80, 81). При этом технические условия на изготовление крышек аналогичны техническим условиям на утолщенные уплотняющие пластины.
В задних крышках насосов подобной конструктивной компоновки размещаются всасывающие и нагнетательные отверстия. При компоновке деталей насоса с центрированием по расточкам корпуса для уплотнения торцов роторов применяются уплотняющие втулки.
Уплотняющие втулки применяются различных конструктивных разновидностей в зависимости от функций, которые они выполняют в насосе. Л
Уплотняющие втулки можно подразделить на: 1
1) втулки, предназначенные только для уплотнения торцов роторов (фиг. 87), которые, в свою очередь, подразделяются на подвижные (при наличии гидравлической компенсации торцовых зазоров) и неподвижные;
2) втулки (неподвижные), во внутренних расточках которых размещаются подшипники качения (фиг. 76);
3) неподвижные втулки, внутренние расточки которых являются опорами скольжения валов роторов (фиг. 45, б);
4) подвижные втулки, представляющие собой опоры скольжения валов роторов, в насосах с гидравлической компенсацией торцовых зазоров (фиг. 45, а).
Общим в конструкциях уплотняющих втулок является наличие плоского параллельного среза на расстоянии от оси, равном половине диаметра начальной окружности и наличие посадочной поверхности, центрирующей втулку в расточке корпуса.
В зависимости от функций, которые уплотняющая втулка выполняет одновременно, в качестве материала для ее изготовления используются антифрикционные чугуны различных марок, закаленная сталь, бронза и разные алюминиевые сплавы.
Техническими условиями на изготовление уплотняющих втулок предусматриваются следующие допуски на обработку:
перпендикулярность уплотняющего торца к оси должна быть в пределах до 0,01 мм на длине по радиусу, равной 50 мм;
параллельность плоскости среза к оси отверстия может отклоняться не более чем на 0,02 мм;
прямолинейность наружной посадочной поверхности должна быть выдержана в пределах отклонений, не превышающих 0,005 мм;
цилиндричность посадочной поверхности может быть с отклонением в сторону овальности или конусности не более чем 0,005 мм;
торцовые поверхности втулок должны быть строго плоскими.
Чистовыми операциями при окончательной обработке наружных и торцовых поверхностей втулок являются шлифование и тонкое точение (при применении бронзы и алюминиевых сплавов). 138
в случаях, когда втулки располагаются в корпусе неподвижно, наружный диаметр выполняется по условиям посадки С .
В насосах с гидравлической компенсацией торцовых зазоров наружный диаметр подвижных втулок должен быть выполнен по условиям посадки X .
9. СПОСОБЫ ГИДРАВЛИЧЕСКОЙ КОМПЕНСАЦИИ ТОРЦОВЫХ ЗАЗОРОВ
Гидравлическая компенсация торцовых зазоров применяется в насосах высоких давлений, имеющих роторы с малым (7-9) числом зубьев и, следовательно, с малыми торцовыми уплотняющими поверхностями и в насосах^ассчитанных на давления 50-100 кГ/см, малой производительности (до 1 л/мин).
Гидравлическая компенсация торцовых зазоров осуществляется следующими тремя способами.
1)Прямой способ компенсации зазоров конструктивно является наиболее простым, так как при этом методе не учитывается переменность давления в торцовых зазорах и поджатие производится по всей площади соприкосновения торцовых поверхностей роторов и уплотняющих деталей. Прижим может быть центральным или периферийным. Однако и в том и в другом случае из-за различия давлений в зонах торцового зазора, примыкающих к камерам нагнетания и всасывания, возможно возникновение перекосов уплотняющих поверхностей деталей, в результате чего появляются
задиры и быстрый износ деталей. Конструкция насоса с прямым центральным прижимом изображена на фиг. 67. Плавающие уплотняющие втулки / прижимаются к шестерням 2 через промежуточные втулки 3 посредством центрально расположенных поршней 4. Усилие прижима создается давлением жидкости, которая подводится к поршням через каналы 6. Роликовые подшипники 7 допускают возможность небольших осевых перемещений плавающих втулок. Диаметры поршней выбираются (экспериментально) из условий создания усилий прижима плавающих втулок к торцам роторов, незначительно превышающих усилия отжима. Изложенный метод компенсации рассчитан и применяется в насосах давлением до 70 кГ/см.
Конструкция насоса с прямым периферийным поджимом уплотняющих втулок изображена на фиг. 89.
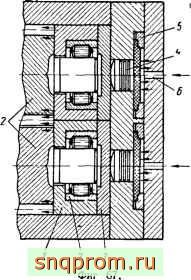
в этой конструкции насоса участки поверхностей плавающих втулок 2, на которые воздействует давление жидкости, ограничены уплотняющими кольцами 8. Жидкость под торцы плавающих втулок подводится из камеры нагнетания в камеру б. Применение подшипников скольжения допускает возможность некоторого осевого перемещения плавающих втулок. Размеры площади поджатия подбираются экспериментально так, чтобы усилие прижима втулок незначительно превышало усилие их отжима. Насос рассчитан на рабочее давление
до 175 /сГ/сл1
Одна из разновидностей конструкций насосов с прямым поджимом втулок показана на фиг. 68. Насос рассчитан на нагнетание небольших объемов жидкости при давлений до 70 кПсм. Уплотнение торцов роторов / осуществляется за счет прогиба бронзовой мембраны 2, на которую давит жидкость, подводимая в камеру 3 из зоны нагнетания. При этом способе уплотнения торцовые зазоры частично выбираются, но в результате неравномерного прогиба мембраны (в центральной части она прогибается больше) происходит неравномерный износ торцов роторов и мембраны.
2) Вторым способом компенсации торцовых зазоров является дифференциальный поджим уплотняющих поверхностей, при котором пытаются учесть характер распределения давления в торцовом зазоре и теми или иными конструктивными приемами устранить тенденцию к перекосу уплотняющих поверхностей деталей. Некоторые конструктивные решения являются довольно сложными. Дифференциальный поджим плавающих втулок показан в конструкции насоса, изображенного на фиг. 90. Плавающие втулки 6 поджимаются к роторам 5 и 11 давлением жидкости, подводимой из камеры нагнетания по каналу 10. Площадь торцовой поверхности втулок, на которую воздействует жидкость, ограничивается величиной зазора а. Величина изолируемой поверхности втулок определяется экспериментальным путем. Недостаток этого способа уплотнения заключается в трудности определения требуемого усилия прижима втулок для разных давлений в связи с изменением закона распределения давления по периферии и торцам роторов. При возрастании рабочего давления зона повышенных давлений может появиться в пределах изолируемого участка торцов
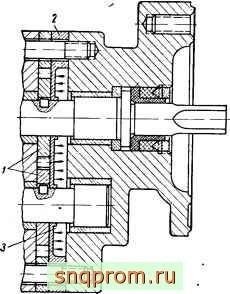
Фиг 68
1 ...
10 11 12 [
13 ]
14 15 16 ...
18