Главная страница сайта
Российские промышленные издания (узловые агрегаты)
1 ...
9 10 11 [
12 ]
13 14 15 ...
18 Конструкция полуоткрытого корпуса с двумя опорами, расположенными в его расточках (фиг. 52), обладает в основном теми же преимуществами, что и конструкция полуоткрытого корпуса, рассмотренная ранее (фиг. 50). К числу главных недостатков здесь также следует отнести сложность обеспечения соосности отверстий под опоры, расположенные вне корпуса с осями расточек под шестерни и опоры, выполненные непосредственно в корпусе насоса.
Кроме того, во избежание увеличения утечек жидкости, требуется иметь острые углы на кромках а (фиг. 50), чего у корпусов из обыч-
Разрез т АЛ
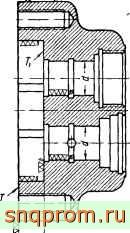
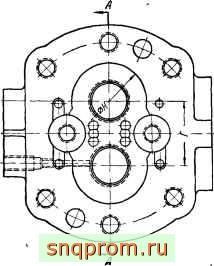
Фиг 52.
ного чугуна трудно достигнуть (чугун в этих местах выкрашивается), поэтому в насосах высоких давлений для изготовления глухих корпусов чугун применяется редко.
Чаще всего для корпусов насосов такого типа используются алюминиевые сплавы. В случаях, когда валы располагаются непосредственно в расточках корпуса, материал его должен соответствовать этим условиям.
В качестве материалов для изготовления корпусов применяются серые чугуны марки СЧ 32-52 и СЧ 21-40 (для насосов небольших давлений), алюминиевые сплавы и стальное литье.
В тех случаях, когда опоры скольжения под валы выполняются в корпусах, в качестве материала для них (корпусов) применяются легированные чугуны и алюминиевые сплавы. Например, корпус насоса высокого давления (140 кПсм), изображенный на фиг. 52, выполнен из алюминиевого сплава с присадками: 5-6% Si; 3-4% Си; 2-3% Ni; 0,5-1% Mg; сотых долей процента; Fe, Мп, Sn и Ti и Al - остальное. При этом твердость Нв рабочих поверхностей
составляет 130-140 единиц. По состоянию поверхности и наличию высокой твердости такую деталь можно получить отливкой в кокиль.
Корпуса некоторых насосов изготавливают из чугуна, который часто имеет следующий химический состав: 1,91% Si; 0,66% Мп; 0,12% Сг; 0,21% Ni; сотых долей процента Ti и V иРе - остальное. При этом твердость нерабочих поверхностей корпуса составляет 207 единиц.
Обычно предъявляют следующие технические требования на изготовление корпусов шестеренных насосов средних и высоких давлений:
1) межцентровое расстояние Г (фиг. 49-52) должно быть выдержано с точностью 0,01-0,02 мм;
2) неперпендикулярность осей отверстий под роторы к торцам Т и Т^ш должна превышать 0,01-0,015 мм на длине по радиусу, равной 100 мм;
3) непараллельность осей отверстий под роторы должна быть в пределах до 0,01 мм на длине Ь;
4) отклонения от цилиндричности расточек под роторы (конусность, овальность, завалы и пр.) не должны превышать 0,01 мм;
5) непараллельность торцовых поверхностей корпуса не должна превышать 0,01 мм;
6) отклонения от соосности отверстий под роторы и расточек под подшипники не должны превышать 0,01 мм;
7) отверстия (колодцы) под роторы (размер Н) должны производиться по системе отверстия А;
8) выпуклость торцов Г и не допускается, а вогнутость допускается в пределах 0,005-0,008 мм по всей поверхности;
9) допуск на глубину колодца назначается в зависимости от необходимой величины торцового зазора.
Эти требования предполагают тщательный контроль основных параметров точности (размеров диаметров, величин отклонения от соосности, величин неперпендикулярности торцов и др.).
Для этой цели применяют различного рода универсальные и специальные контрольно-измерительные приспособления. На одном из заводов серийного производства насосов для измерения межцентрового расстояния расточек применяется приспособление, изображенное на фиг. 53. Измерения производятся с помощью рычажного индикаторного устройства с точностью в пределах 0,005-0,01 мм. Показания этого приспособления учитывают также фактическое отклонение величин диаметров колодцев.
Вначале приспособление настраивается на номинальный размерЛ между наружными стенками и на размер В между внутренними стенками колодцев. Затем устанавливают изделие, прижимая наружную стенку одного из колодцев к неподвижному штырю и при помощи рычагов (на фиг. 53 не показан) сжимают пружину 6. После определения (по индикатору) фактического отклонения размера Л от номинального поворотом рукоятки специальной пружины 7освобождается пружина 6, а планка 2 перемещается в противоположную сторону до упора обоих штырей во внутренние стенки колодцев. Индикатор 122
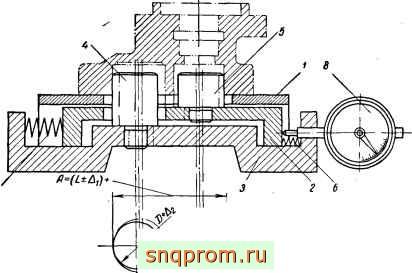
Ли/ к: .
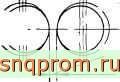
Фиг. 53. Приспособление для измерения межцентрового расстояния 1 в корпусах насосов.
Л-hir-tf
1 г 7
. I
Фиг. 54. Приспособление для контроля перпендикулярности образующей расточек и стыковой площади в корпусах насосов. ,

показывает фактическое отклонение размера В. Фактическое расстояние между центрами колодцев Г = 0,5 (Л + В).
Контроль перпендикулярности образующей колодцев к плоскости стыка корпуса выполняется при помощи специальных индикаторных приспособлений. Одно из них изображено на фиг. 54. Приспособления этого типа настраиваются по эталонному кольцу. Изделие устанавливают на плоскость приспособления, причем неподвижный штифт 1 и конец подвижного рычага 2 должны войти в измеряемый колодец. Перемещая деталь по плоскости приспособления, отжимают конец рычага до упора стенки колодца в штифт /. При этом индикатор 3 показывает отклонение образующей колодца от перпендикуляра к плоскости разъема. Для измерения этого отклонения по всему периметру деталь поворачивают вокруг оси колодца на 360°.
6. ВЫБОР ВЕЛИЧИН ЗАЗОРОВ МЕЖДУ ПОВЕРХНОСТЯМИ РОТОРОВ И КОРПУСА
Исследованиями установлено [16], [39], что основной долей объемных потерь в шестеренных насосах являются утечки жидкости через торцовые зазоры. В связи с этим нет необходимости чрезмерно ограничивать величину радиального зазора, а рекомендации в отношении его величины, изложенные в литературе прошлых лет [2], [9], [29], следует считать устаревшими. Изучение новых конструкций шестеренных насосов (иностранных и отечественных) показывает, что величины радиальных зазоров для насосов с рабочим давлением до 140 кГ/см не принимаются меньшими, чем бр > 0,0015Dg.
При такой величине радиального зазора потери мощности на вязкостное трение между поверхностями головок шестерен и расточек корпуса также становятся незначительными, так как они обратно пропорциональны величине радиального зазора в первой степени. Следовательно, наибольшее влияние на характеристику насоса оказывает величина торцового зазора б„.
В работе W. Е. Wilson [50] предложена методика расчета величины оптимального зазора между перемещающейся (вращающейся) и неподвижной поверхностями, основанная на предположении, что вся энергия, расходуемая на вязкостное трение, переходит в тепловую и сохраняется в жидкости. При этом величина оптимального зазора соответствует наименьшим потерям мощности (вследствие утечек жидкости и вязкостного трения). Этот метод, построенный на основе ряда допущений, следует, разумеется, применять для ориентировочных и предварительных расчетов. Вместе с тем результаты расчетов по этому методу являются удовлетворительными в большом числе практических случаев.
Для облегчения анализа величин при определении торцовых зазоров на фиг. 55 изображена кривая зависимости потерь мощности от относительной величины зазоров. Кривая свидетельствует о том, что если величины зазоров меньше оптимальных, например, в два раза, то потери мощности будут меньше, чем в случаях, когда зазоры больше оптимальных тоже в два раза. Это особенно важно 124
для шестеренных насосов, где предпочтение отдается величине объемного к. п. д. (перед эффективным к. п. д.) и когда применение малых зазоров оправдывается. Стоимость нагнетания в этих случаях в большей степени определяется объемными потерями, в меньшей - механическими.
Для предварительного выбора величины торцового зазора пользуются номограммой, изображенной на фиг. 56.
Окончательная величина торцового зазора принимается обычно компромиссным решением исходя из стремлений получения и поддер-
Ш%300
II во SB 0
II О
It в
0,002(1004 0,01 0,02 0,040,060.1 0,2 0,40,6 I 2 34 бВЮбф/йоп^ Отношение фактических зазоров к оптимальным
Фиг. 55. Кривая потерь мощности при фактических и оптимальных торцовых зазорах.
жания желаемой величины торцового зазора при наименьшей стоимости и достижения при этом высоких показателей работы насоса в возможно большем диапазоне эксплуатационных условий.
Во всяком случае величина зазора должна быть такой, при которой было бы возможно компенсировать неизбежные погрешности изготовления и монтажа основных деталей насоса и гарантировать его надежную работу без заеданий и преждевременного износа сопряженных поверхностей.
Как показывает практика конструирования и эксплуатации, суммарный (на обе стороны) торцовый зазор в насосах без гидравлической компенсации не должен быть меньше 0,02 мм.
7. ЗАЩЕМЛЕНИЕ ЖИДКОСТИ В МЕЖДУЗУБОВОМ ПРОСТРАНСТВЕ И РАСЧЕТ СИСТЕМЫ КАНАЛИЗАЦИИ
Ранее установлено, что изменение объема отсеченного междузубового пространства, происходящее в ходе зацепления пары зубьев, контактирующихся обеими сторонами (при беззазорном зацеплении) или при одновременном контактировании двух пар зубьев (в случае
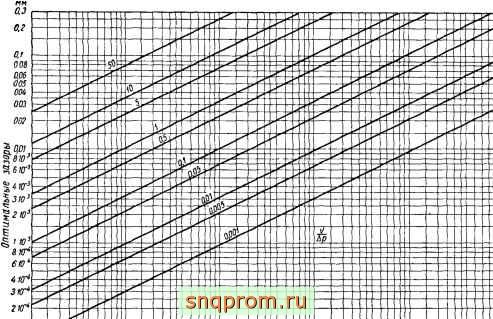
llff*.
0 г 3 i S67S w 20 30 io 50 70 100 300 300 sooimiooo гтзт sim miyomkooo,0000 m* Фиг 56 Номограмма для определения величины торцового зазора.
зацепления с боковым зазором) сопровождается соответствующим изменением давления в этом пространстве. Возникающая при этом пульсирующая нагрузка на опоры и зубья роторов достигает значительных размеров и является причиной их преждевременного износа, увеличения потерь мощности и ухудшения коэффициента полезного действия насоса.
Кроме того, в конце периода существования отсеченного междузубового пространства возникает кавитация (в связи с увеличением объема) вследствие расширения примешанного к жидкости воздуха и выделения газовой составляющей. Междузубовая впадина в этих условиях заполняется жидкостью лишь частично, что вызывает дополнительный шум при работе насоса.
Для устранения упомянутых явлений применяются различные конструктивные приемы, смысл которых сводится либо к соединению отсеченного пространства с камерами нагнетания или всасывания, либо к изменению параметров зацепления с целью уменьшения коэффициента перекрытия до значений, близких к единице
Способы разгрузки защемленного пространства посредством канализации жидкости
Некоторое ослабление компрессии жидкости (как положительной так и отрицательной ) в отсеченном междузубовом пространстве может быть достигнуто соответствующим изменением отдельных параметров зацепления.
Для данного числа зубьев с увеличением угла зацепления или уменьшением рабочей высоты зуба снижается величина коэффициента перекрытия е, и следовательно, зависящая от него степень защемления. Однако эффективность этого мероприятия невелика потому, что даже при небольших значениях е наблюдается заклинивание жидкости. Кроме того, снижению коэффициента е препятствует возникающее при этом заострение зубьев (при малых числах зубьев и больших углах зацепления), а уменьшение рабочей высоты зубьев снижает геометрическую производительность насоса.
Еще менее эффективны эти способы в случае беззазорного зацепления, где, как известно, защемление жидкости имеет место даже при Е = 1.
Среди мер, направленных против защемления жидкости, наибольшее распространение получил метод канализации жидкости. Для этой цели на торцах уплотняющих втулок или прокладок (фиг. 59, 61, 62) фрезеруют специальные канавки
Канализация с помощью радиальных сверлений в междузубовых впадинах (фиг. 57) и зубьях (фиг. 58), хотя и эффективна, но применяется реже, так как это усложняет конструкции насосов.
Имеющиеся в существующей специальной литературе рекомендации относительно выбора размеров и расположения разгрузочных канавок подлежат уточнению с учетом влияния такого важного эксплуатационного параметра, как скорость вращения роторов.
Наличие в зацеплении бокового зазора при коэффициенте перекрытия Е > 1 теоретически требует такого расположения канализационных канавок, при котором отсеченное междузубовое пространство соединялось бы с зоной нагнетания лишь на время уменьшения своего объема, а в последующий период, когда объем увеличивается, связывалось бы с зоной всасывания. Это требует расположения канавок на расстоянии от линии центров, которое соответствует симметричному расположению точек контакта профилей на линии зацепления (фиг. 59, 61, а). При этом назначением одной канавки является устранение компрессии, а назначением другой - предотвращение
кавитации. Однако путем осцил-лографирования давления в зоне защемления (фиг. 60) была выявлена недостаточная эффективность этого метода разгрузки. В исследуемом насосе имели место значительные торцовые зазоры (порядка 0,07-0,075 мм на сторону), а значения давления в защемленном пространстве превышали рабочие давления. Даже при нулевом рабочем давлении (фиг. 60) величина давления в защемленном пространстве достигала 7 кГ/см. Эффект компрессии был бы более заметным при меньших (нормальных) величинах торцовых зазоров. Кроме того, очевидно, что в исследуемом случае размеры канавок, подводящих масло в отсеченное пространство были недостаточны, что отрицательно сказывается на всасывающей характеристике насоса и влечет за собой появление кавитационного шума.
С целью улучшения системы отвода и подвода жидкости необходимо изыскивать возможности увеличения эффективного сечения канавок (фиг. 61, а). Для этого предпринимаются различные конструктивные меры. Канавки располагают по дуге, как это показано на фиг. 61, б, или увеличивают полезную площадь сечения, придавая канавке форму скоса (фиг. 62). В этом случае площадь сечения увеличивается, но она, как показывают расчеты, все же является недостаточной.
При расчете сечения канавок, предназначенных одновременно и для подвода жидкости в междузубовое пространство из камеры всасывания, скорость течения (жидкости) не должна приниматься более 4-5 м/сек.
Выполнение разгрузочных канавок в форме скоса (фиг. 62) приводит к нарушению герметичности камер нагнетания и всасывания. Прочерчивание участка зацепления (в масштабе 20 : 1) показывает, что в момент симметричного расположения точек контактирования зубьев на линии зацепления камеры нагнетания и всасывания
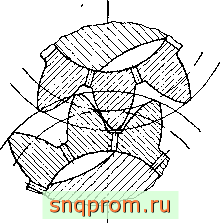
Фиг. 57.
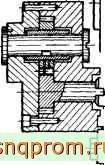
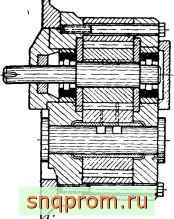
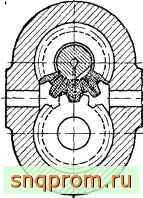
Фиг. 58.
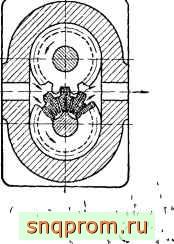
9 Рыбкин и Усов 88
Соединяются через зону зацепления щелями размером около 0,01 т^.
Для более полного сочетания служебных функций канавок, одновременно предотвращающих компрессию и кавитацию, целесообразно осуществлять такую канализацию жидкости, при которой отсеченное междузубовое пространство непрерывно соединяется с зоной нагнетания. Для этого необходимо наличие односторонней торцовой канавки, направленной в сторону нагнетания и расположенной на расстоянии
с = -- (2- e)cosa
от линии центров (фиг. 63).
Таким путем достигается значительное увеличение эффективной площади сечения канализационной канавки и обеспечивается подвод жидкости в отсеченное пространство в течение всего периода увеличения его объема. Наличие такой канавки позволяет полностью устранить опасность возникновения местной кавитации в отсеченном междузубовом пространстве, которое при этом приходит в зону всасывания полностью заполненным.
Это в некоторой степени снижает производительность насоса, но вполне оправдывается результатами канализации жидкости Дальнейшее увеличение рабочей площади сечений разгрузочных канавок невозможно без нарушения изоляции камер нагнетания и всасывания и возникновения перетока жидкости между этими камерами через отсеченное пространство. Условия канализации жидкости могут быть улучшены лишь в результате снижения скорости вращения роторов или уменьшения их ширины, что привело бы к потере производительности насоса.
Система канализации жидкости с помощью радиальных сверлений (фиг. 57, 58) позволяет получить размеры каналов, обеспечивающие надежность разгрузки, но, к сожалению, технологическая сложность такой системы канализации не стимулирует ее применение и является поводом для изыскания других способов устранения возможности защемления жидкодти в отесеченном междузубовоМ пространстве.
J Расчет канализационных сечений
Площадь сечения каналов должна обеспечивать (в любой момен! существования отсеченного междузубового пространства) истечении жидкости со скоростью, не превышающей допустимых величин! 130
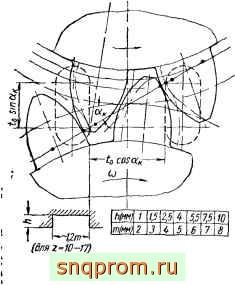
Фиг. 59
1 ...
9 10 11 [
12 ]
13 14 15 ...
18