Главная страница сайта
Российские промышленные издания (узловые агрегаты)
1 ...
8 9 10 [
11 ]
12 13 14 ...
18 ,



Ведущий ва/!
Ведомый ва/1
ведущего и ведомого роторов.
использованием проставочных колец и радиально упорных двухрядных подшипников с разрезным наружным кольцом. С целью получения одинаковых торцовых зазоров шестерни жестко фиксируются на валах в осевом направлении. Специальные подшипники, изготовленные из высоколегированных материалов, выдерживают нагрузки при давлениях до 140 кПсм.
Однако применение в этой компоновке обычных стандартных подшипников (при увеличенных габаритах роторов) обеспечивает работу насосов с давлением лишь до 25 кГ/см. Монтаж опор при конструктивной компоновке (в) затрудняется в связи с необходимостью точной пригонки проставочных колец по ширине.
Малые габариты и высокая грузоподъемность игольчатых подшипников позволяют широко использовать их в качестве опор в шестеренных насосах. На фиг. 46, г изображена компоновка игольчатых подшипников с наружным и внутренним кольцами в шестеренном насосе среднего (до 32 кГ/см) давления. Здесь шестерни жестко фиксируются на валах при помощи пружинных колец и проставок, ограничивающих перемещение валов в осевом направлении в пределах торцовых зазоров.
Компоновка ведущего вала в роликовом и двухрядном роликовом самоустанавливающемся подшипниках (фиг. 46, д) допускает небольшую несоосность расточек корпуса под подшипники. Шестерня свободно сидит на валу (и шпонке), но фиксируется в осевом направлении проставочными кольцами и прессовой посадкой внутренних колец подшипников. Осевое смещение вала предупреждается роликовым самоустанавливающимся подшипником. Такое сочетание опор вала применяется в насосах среднего давления. Ведомая шестерня вращается на консольной оси на роликовом двухрядном самоустанавливающемся подшипнике. Консольная ось применяется в насосах сравнительно редко, потому что при больших нагрузках во избежание перекосов приходится увеличивать диаметр вала и, следовательно, габариты подшипников и шестерни. Вместе с тем консольный монтаж ведомой шестерни позволяет несколько упростить конструкцию насоса.
Применение в качестве опор ведущего и ведомого роторов шестеренного насоса (фиг. 46, е) конических роликовых подшипников позволяет (при жесткой фиксации на валу шестерен в осевом направлении) получить одинаковые торцовые зазоры. Грузоподъемность конических роликовых подшипников допускает применение их в насосах среднего и высокого давлений. Недостатком этой компоновки опор является сложность монтажа подшипников, недопускающих излишней перетяжки и слишком больших радиальных зазоров.
Наиболее часто для шестеренных насосов высоких давлений применяются подшипники скольжения. Для восприятия радиальных усилий от привода на ведущем валу применяется сочетание шарикового (или роликового) подшипника с подшипников скольжения (фиг. 46, ж). В такой компоновке производится прессовая посадка шестерен на валы. К недостаткам следует отнести необходимость назначения очень жестких допусков на точность изготовления под-
шипников скольжения, а также необходимость применения прецизионного подшипника качения. Но при такой компоновке применение стандартных подшипников качения с обычной точностью изготовления может привести к появлению кромочных давлений в подшипниках скольжения из-за больших радиальных зазоров, что приводит к заеданию подшипников скольжения и выходу из строя насоса.
Для восприятия больших радиальных нагрузок от привода в насосах высокого давления (без прогибов ведущего вала) используется компоновка опор (фиг. 46, з) с применением двухрядных самоустанавливающихся шарикоподшипников. Крутящий момент на ротор здесь передается муфтой с крестообразным вырезом. Это допускает небольшой перекос и несоосность валов. Осевые перемещения валов ограничены шестернями, зафиксированными пружинными кольцами.
Валы ведомых роторов вращаются в подшипниках скольжения. Недостатком компоновки (фиг. 46, з) является некоторое усложнение конструкции насоса и увеличение его габаритов.
Компоновка опор роторов с валами, изготовленными заодно с шестернями при применении подшипников скольжения, изображена на фиг. 46, и. Здесь перемещение валов ограничено пределами торцовых зазоров между шестернями и уплотняющими деталями. Точность изготовления таких опор находится в пределах 1-го класса.
На фиг. 46, к изображена компоновка ведущего вала на консоли в подшипнике скольжения. Для восприятия радиальных нагрузок от привода применяется роликовый подшипник. Передача крутящего момента производится при помощи шипа и паза в валах. Консольное расположение шестерни требует применения подшипника скольжения увеличенной длины (вследствие больших нагрузок), изготовление и монтаж которых влечет за собой значительные технологические трудности. Ведомая шестерня с впрессованной в нее бронзовой втулкой вращается на валу (оси).
На фиг. 46, л изображен один из вариантов компоновки ведущего и ведомого валов насоса среднего давления (25-32 кГ/см) на игольчатых подшипниках. В отличие от компоновки опор, показанной на фиг. 46, г, здесь внутренней беговой дорожкой для иголок является поверхность вала, а наружной беговой дорожкой - поверхность отверстий уплотняющих элементов. Недостатком конструкции является необходимость изготовления деталей подшипников по высокому классу точности с применением легированных материалов и точного расчета диаметров дорожек с целью получения минимального зазора между иглами.
Применение свободных иголок требует их тщательной селекции, так как размеры диаметров иголок могут быть различны. Это приводит к увеличенной нагрузке на иглы, к перекосу и интенсивному износу игл и к заеданию подшипника.
Нафиг. 46, ж показана компоновка ведущего вала с роликовыми подшипниками, имеющими конструкцию, предохраняющую вал от осевых перемещений. В посадочное отверстие ведомой шестерни, вращающейся на неподвижной оси, запрессована бронзовая втулка.
8 Рыбкин и Усов 88 < 113
Потери на трение в подшипниках
Потери на трение в подшипниках скольжения, работающих в условиях жидкостного трения, почти не зависят от нагрузки и пропорциональны вязкости жидкости и скорости вращения.
Для вычисления момента трения подшипника в этом случае может быть применена формула И. Н. Петрова
3,36.10- ti . 0,55(4)-4q,]4, (123)
М
тп (ск) -
где / - длина подшипника в мм; d - диаметр вала в мм; 6 - диаметральный зазор в мм;
р. - вязкость масла при рабочей температуре в сантипуазах; Qi - нагрузка на подшипник в кГ.
Величина (d/iy- вводится в формулу только, когда ->1-При значительном числе оборотов и небольшой нагрузке (при > 150, где р - удельное давление в кГ/см, момент трения можно с достаточной точностью вычислять по формуле
M ;3,36.10- ijin--. (124)
В нормально работающих подшипниках скольжения величина к. п. д. составляет обычно 0,97-0,99.
При наличии кромочных давлений действительные потери на трение могут оказаться выше вычисленных по приведенным выше формулам.
Потери на трение в подшипниках качения складываются из постоянных потерь при отсутствии нагрузки и переменных потерь, которые следует считать пропорциональными нагрузке.
Постоянные потери, вызываемые главным образом трением о сепаратор и сопротивлением, связанным с наличием масла, зависят от типа и размеров подшипника, конструкции сепаратора и точности монтажа.
Переменные потери (при данной нагрузке) зависят, в основном, от типа подшипника. Эксперименты показывают, что сила трения в подшипнике связана с нагрузкой линейной зависимостью (в зоне допустимых нагрузок). С увеличением вязкости масла и скорости сила трения в подшипнике возрастает.
При прочих одинаковых условиях наименьшее трение имеет место в цилиндрических роликоподшипниках и сферических шарикоподшипниках. Несколько большее трение наблюдается в радиальных однорядных шарикоподшипниках.
В конических и сферических роликоподшипниках трение значительно больше. Наиболее неблагоприятными в отношении трения являются игольчатые подшипники.
Различие в потерях на трение для разных типов подшипников определяется также их неодинаковой чувствительностью к точности моцтажа. Начальную силу трения можно считать пропор-
циональной диаметру подшипника. С увеличением числа шариков или роликов потери на трение возрастают. При увеличении зазора трение в подшипнике сокращается за счет уменьшения влияния перекосов вследствие лучшей самоустанавливаемости подшипника.
Для расчета момента трения в подшипнике качения можно пользоваться формулой
W = Л1 ( + (2, = Т^ г, + f Q,r (125)
где Тд - сила трения в кГ на плече, равном радиусу вала при отсутствии нагрузки; / - удельный коэффициент трения, равный отношению приращения силы трения к приращению нагрузки; - нагрузка в кГ; Гд - радиус вала. Значения / и Тд берутся в табл. 5 (для скорости вращения до 3000 об/мин.):
Таблица б
Типы подшипников | /п | Топ |
Однорядные радиальные шариковые подшипники | 0.001 | 0,015 |
Цилиндрические роликовые и сферические шариковые подшипники | 0,0008 | 0,015 |
Конусно-роликовые и сферические роликовые | 0,002 | 0,075 |
Упорные шариковые | 0,0015 | 0,15 |
5. КОРПУСА НАСОСОВ
При конструировании корпуса насоса необходимо рассчитать размеры подводящих каналов и установить конфигурацию рабочих камер, произвести расчет на прочность стенок корпуса (в случае необходимости), определить материал, установить технические требования и выбрать вариант внешнего конструктивного оформления корпуса.
Все связанные с конструированием вопросы должны рассматриваться с учетом предполагаемых условий эксплуатации насоса.
Конфигурация рабочих камер и расчет сечений всасывающего и нагнетательного отверстий
Разнообразие эксплуатационных требований к насосам привело к созданию большого числа различных по конструкции корпусов. При определении размеров и конфигурации рабочих камер насоса необходимо руководствоваться установленными ранее зависимостями величины нагрузки на опоры и всасывающей характеристики насоса
8* 115
от размеров рабочих камер. Необходимо также предусматривать возможность реверсивной работы насоса. В этом случае камеры всасывания и нагнетания должны быть аналогичны по конструкции.
Наиболее часто применяется конфигурация камер всасывания и нагнетания, изображенная на фиг. 47. Угол Pj, определяющий размеры рабочих камер, колеблется в пределах 45°-86° и условно отсчитывается от линии центров роторов по направлению к их горизонтальным осям. Для увеличения размеров уплотняющей дуги рекомендуется уменьшать значение р^ в указанных пределах (при уменьшении числа зубьев шестерен и возрастании давления).
При конструировании насосов низкого давления обычно применяют симметричные камеры всасывания и нагнетания с углом Pi, Не превышающим 75-80° (фиг. 47). Размер А ширины камеры выбирают из расчета Л = 6 -f (4 - 6) мм.
При конструировании нереверсивных насосов среднего и высокого давлений камера всасывания часто выполняется с углом Pz, равным 90°. При такой конфигурации камер всасывания улучшаются условия заполнения междузубовых впадин. В порядке опыта угол Рг камеры всасывания был изменен с 76 до 90°. В результате сопротивление в камере всасывания уменьшилось с 178 до 127 мм рт. ст При числе зубьев у роторов 12 -~ 18 можно допускать расширение камеры всасывания путем увеличения угла Рг примерно до 105-120°.
С целью уменьшения нагрузки на опоры камеру нагнетания выполняют в виде узкой щели. На фиг. 47 эта щель определяется углами Pg.
Известно, что в шестеренных насосах ведомый ротор нагружен больше, чем ведущий. Для уравновешивания нагрузки на роторы ось симметрии всасывающих и нагнетательных камер смещается в сторону ведущего ротора примерно на /g ширины. На фиг. 47 положение этой щели определяется углами Рз и р^.
Выбор диаметров отверстий и проходных сечений (размеры D g, Dgc) для камеры всасывания производится с учетом скорости течения жидкости (производительности насоса), которая не должна превышать 1-2 м/сек. При расчете диаметров отверстий и проходных сечений камеры нагнетания рекомендуется допускать скорость течения масла не выше 3-5 м/сек для насосов низкого давления и 5-6 м/сек для насосов высокого давления. .
116 I
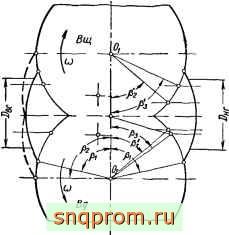
Фиг. 47. Параметры всасывающих и нагнетательных камер.
о
р
СЭО Оо Oi VJi
Скорость V в м/сек с;
VOOO Oi <л
11111 м 111111111 I I I I-
-рекоменди-
емыа диапазон скоростей в нагнетательном трубо прободе (попости насоса)
- рекомендуемый диапазон скороа 00 всасыбающвм трубопроВоое (полости насоса)
:твй
It р x о
S S тз б
Щ
Внутренний диаметр трдбопродода д дюйма/.
§5
| 1 1 1 | | 1 1 1 | | | -1г 1 1 1 1 | - -1г -1г | IIII | lllllnli | *1Г 1111 | | | | |
| | | | | | | 1 1 1 1 11111 | | | | | | | |
Диаметр проходного сечения полости насоса 6 мм
IMI МП
Производительность насоса б л/мин +
Для удобства определения размеров отверстий камер всасывания и нагнетания в зависимости от производительности насоса можно пользоваться номограммой, приведенной на фиг. 48.
Указания по расчету на прочность
. Расчет толщины стенок корпусов насосов производится редко и только в насосах высокого давления исходя из величин пробных давлений и выбранного материала корпуса. Соотношения величин пробных и рабочих давлений при этом принимаются согласно табл. 6.
Величина напряжения в стенках кор-Таблица 6 У^а рассчитывается по формуле
При рабочем давлении
Пробное (расчетное) давление
80 КГ.СМ
150 кГ/с/<2
где а < од.
Здесь R
наружный радиус корпуса в см;
радиус окружности головок шестерен в см; допускаемое напряжение растяжения в кГ/см; а - напряжение во внутренних волокнах стенок корпуса в кГ/см; р„г - внутреннее давление жидкости в кГ/см (максимальное пробное давление, на которое рассчитывается насос).
При расчете корпусов насосов можно пользоваться следующими данными по допускаемым напряжениям: для бронзы ор < 600, для чугуна ор < 600, для стального литья ор < ПОО, для алюминиевого литья ор < 400 кГ/см. Для уменьшения резонирующего эффекта, возникающего в результате вибраций стенок корпуса, толщина их обычно увеличивается против требуемых по расчету.
* Конструктивное оформление корпусов, материалы и технические условия
В зависимости от общей конструктивной компоновки насосов их корпуса выполняются открытыми и полуоткрытыми, с центрированием деталей по расточкам корпуса (пакетный принцип монтажа) или с фиксацией относительного положения деталей посредством контрольных штифтов, шпилек и специальных болтов.
Преимуществами конструкций открытых корпусов при пакетном способе монтажа деталей (насосы конструкции завода Гидропривод , ЭНИМС и др.) являются: простота технологии изготовления и получения необходимой осевой точности расположения отверстий и пер-118
пендикул яр ности осей отверстий под шестерни и втулки к торцам Т корпуса (фиг. 49).
Недостатком этого типа корпусов следует считать необходимость получения размера Ь по высокому классу точности с целью обеспечения гарантированных зазоров между торцами роторов и уплотняющих втулок.
Корпуса этого вида обычно выполняют с лапами для крепления насоса. Вместе с тем имеются конструкции корпусов и с фланцевым креплением. Крышки крепят винтами. Отверстия для крепления трубопроводов у чугунных и у стальных корпусов делают с кони-
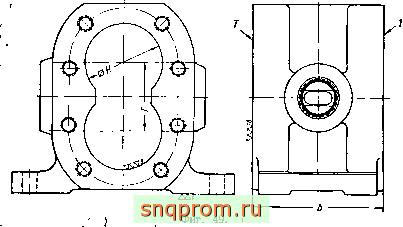
ческой или (трубной) цилиндрической резьбой (у насосов с производительностью до 200 л/мин). У насосов с производительностью выше 200 л/мин применяют фланцевое присоединение трубопроводов.
У алюминиевых корпусов в отверстиях для трубопроводов, как правило, делают трубную цилиндрическую резьбу. Вместе с тем применяется и фланцевое присоединение (на шпильках) трубопроводов к корпусам насосов.
Применение конструкций корпусов полуоткрытого типа при пакетном принципе монтажа (фиг. 50) позволяет несколько сократить габариты насоса за счет передней крышки. При этом сокращается время, необходимое на обработку корпуса, так как необходимость в крепежных отверстиях под переднюю крышку, отпадает, в результате отсутствия стыка между передней крышкой и корпусом повышается герметичность насоса.
Недостатком этой конструкции является технологическая сложность обработки глухих отверстий под пакеты шестерен с втулками, связанная с необходимостью получения в жестких пределах перпендикулярности торцов Т, по отношению к осям отверстий для роторов и обеспечения параллельности торцов Т и Т^.
Отверстия для трубопроводов всасывания и нагнетания размещаются в корпусе этого типа с боковых сторон (так же как и в первом случае). Крепление насоса, как правило, фланцевого типа.
Открытый корпус с центрированием деталей посредством штифтов и шпилек, помимо указанных ранее преимуществ, отличается еще и тем, что гарантированный зазор между торцами шестерен и уплот-
Л
РазрезтДй
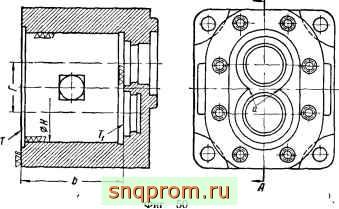
няющими боковыми пластинами здесь достигается значительно проще в результате того, что размерная цепь включает лишь две величины:
ширину корпуса и ширину РазрезпоЛР ерни. Вместе с тем при-менение открытых корпусов с центрированием деталей посредством штифтов и шпилек усложняет сборку насосов, которая обусловливается необходимостью получения соосности отверстий (под роторы и опоры), расположенных в двух различных деталях.
Кроме того, технология обработки корпуса в этом случае усложняется необходимостью соблюдения строгой перпендикулярности торцов Т к осям отверстий под роторы. Отверстия под винты делаются, как правило, сквозными, а отверстия под шпильки развертываются присборке. При небольшой ширине корпуса (фиг. 51) всасывающие и нагнетательные отверстия размещаются в крышках (одно с правой стороны вала, другое - с левой).
Значительно реже оба канала располагаются в приливах по боковым сторонам задней крышки (см. фиг. 84). - 120 . .
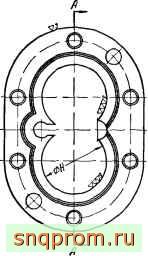
Фнг. 51.
1 ...
8 9 10 [
11 ]
12 13 14 ...
18