Главная страница сайта
Российские промышленные издания (узловые агрегаты)
1 ...
7 8 9 [
10 ]
11 12 13 ...
18 а) определение напряжений изгиба в опасных сечениях с учетом знакопеременности нагрузки и концентрации напряжений;
б) определение наибольших величин прогиба вала с учетом характера распределения нагрузки;
в) вычисление величин углов поворота (перекоса) осей валов в подшипниках;
г) определение напряжений кручения в опасном сечении с учетом цикличности нагрузки и расчетом угла закручивания. При расчете осей обычно определяется величина прогиба с целью предотвращения возможности заклинивания зубчатой пары.
Особо тщательными и ответственными должны быть расчеты прогиба валов и углов поворота (перекоса) в опорах в случае применения в насосе подшипников скольжения.
Во избежание нарушений нормальной работы подшипников и появления кромочных давлений допускаемые величины прогиба
должны быть меньше величин зазора ~, который определяется
зависимостью = 0,001-0,003.
Допускаемые величины прогиба валов в случае использования подшипников качения (за исключением игольчатых подшипников) немного больше, чем при применении подшипников скольжения, но и они не должны превышать 0,015-0,025 мм. При этом угол поворота (перекоса) валов в опорах не должен превышать 0,0005- 0,001°. При большем же возникает опасность заклинивания тел качения в подшипниках.
Наиболее чувствительными к возможным перекосам валов являются игольчатые подшипники, что требует при их применении особо тщательных расчетов. Прогибы валов выше допустимых вызывают увеличение удельного давления по краям беговых дорожек, что ведет к быстрому износу игл и поверхностей дорожек.
Величина угла закручивания при наибольшем крутящем моменте не должна превышать одного градуса на длине, равной 20-25 диаметрам вала.
Материалы и технические условия на изготовление валов
Тип применяемых подшипников определяет комплекс технологических требований, предъявляемых к валам. К их числу относятся: выбор материала и метода его термической обработки, характер отдельных операций и точность обработки.
В случае применения подшипников скольжения материал валов, поверхностная твердость опорных шеек и степень чистоты обработки должны отвечать всем требованиям сопряженных пар скользящих опор, работающих в определенных условиях.
Для изготовления валов применяются главным образом легированные стали: 20Х, 12ХН2, 12ХНЗ, 18ХНВА и 13ХНВА, которые подвергаются цементации и последующей закалке до поверхностной твердости Rc порядка 62-64.
Аналогичные марки сталей с соответствующей термообработкой применяются для изготовления валов с шейками, представляющими беговые дорожки под иголки или ролики подшипников качения. Иногда для этих целей применяют азотируемые стали: 38ХМЮА, j 40ХЮ и 35ХЮА. 1
В насосах с подшипниками качения валы изготовляются обычно из стали марки 40Х и простой конструкционной стали марки 45 с последующей термической обработкой до получения поверхностной твердости Rc порядка 54-56.
Наибольшее распространение при термической обработке валов получили закалка токами высокой частоты (ТВЧ) и закалка с нагревом в печи и охлаждением в масле (во избежание появления трещин и короблений).
Для валов, работающих на подшипниках скольжения, очень важное значение имеет чистота обработки и качество поверхности опорных шеек.
Для увеличения срока службы подшипников шейки валов после термической обработки шлифуются, а затем полируются или притираются, либо подвергаются суперфинишной отделке в зависимости от окружной скорости на шейках и прочих условий работы. ,
Технические условия на валы включают обычно следующие требования:
а) допустимые отклонения тела вала от правильной геометри- ческой формы (конусность и овальность) не более 0,005 мм;
б) чистота и твердость поверхностей опорных шеек, согласно ГОСТу 2789-59;
в) биение мест посадки ротора относительно опорных шеек не должно превышать (0,3-0,35) 6 ;
г) посадки для сопряжений с деталями, сидящими на валах (роторами, подшипниками и др.) должны назначаться по конструктивным соображениям;
д) биение выходного конца приводного вала относительно опорных шеек не должно превышать 0,02-0,04 мм.
4. ОПОРЫ ВАЛОВ (ПОДШИПНИКИ)
в шестеренных насосах среднего и высокого давления опоры валов являются более нагруженными в сравнении с опорами других типов гидронасосов, работающих в аналогичных эксплуатационных условиях. Вместе с тем опоры должны обеспечивать работоспособность насоса в течение всего гарантированного срока службы при всех режимах, предусмотренных техническими условиями. Основные требования, предъявляемые к опорам валов следующие:
1) малые размеры диаметров вследствие ограниченности пространства для размещения подшипников;
2) долговечность работы порядка 5000-6000 час;
3) высокая степень точности в радиальном и осевом направлениях;
1П2
4) простота сборки и разборки;
5) экономичность технологии изготовления и эксплуатации.
В шестеренных насосах применяются опоры скольжения и качения.
Выбор типа опоры зависит от очень большого числа факторов. Предпочтение тому или другому типу подшипников должно строго обосновываться в каждом отдельном случае.
Большими преимуществами подшипников качения являются возможность их приобретения на стороне в готовом виде и простота монтажа. Существенным недостатком их являются сравнительно большие габариты, что в ряде случаев исключает возможность их встройки без значительного увеличения размеров насоса.
Применение подшипников скольжения позволяет сконструировать насос с гораздо меньшими габаритами, но требует более высокой квалификации рабочих и применения цветных металлов, повышающих стоимость насоса. При ограниченных межцентровых размерах и высоких рабочих давлениях предпочтение отдается подшипникам скольжения потому, что подобрать подшипники качения требуемой грузоподъемности для этих условий не всегда возможно.
Подшипники качения
В шестеренных гидронасосах применяются подшипники качения (различных типов) лишь в случаях, когда позволяют габариты насоса (межцентровое расстояние роторов). Но так как к шестеренным насосам, как и к большинству других узлов гидросистемы, подлежащих встройке в станки, предъявляются жесткие требования в отношении их габаритов, то это значительно ограничивает применение подшипников качения. Имеется немного конструкций насосов, роторы которых смонтированы на шариковых или роликовых подшипниках (фиг. 87, 74).
Вместе с тем в последнее время начинают широко применяться игольчатые подшипники, обладающие малыми габаритами и большой грузоподъемностью. Отрицательными качествами этих подшипников следует считать высокую степень чувствительности к монтажным погрешностям и относительно высокую стоимость. Но игольчатые подшипники обладают важными преимуществами перед подшипниками скольжения. Они способны работать в значительно более широком диапазоне температур и скоростей, чем подшипники скольжения. Игольчатые подшипники могут быть свободно заменены подшипниками скольжения без изменения конструкции.
Как свидетельствуют испытания [26], хорошие результаты дает применение игольчатых подшипников, в которых иглы заключены в сепараторы. Такие подшипники обладают большей грузоподъемностью, монтаж их значительно проще, так как эти подшипники менее чувствительны ко всякого рода монтажным погрешностям и неточностям изготовления
Следует отметить, что нагрузочная характеристика игольчатых подшипников связана с их габаритами не прямой зависимостью, поэтому применение их в насосах высокого давления (до 100 кГ/см)
целесообразно только при малой производительности насоса. В этом случае можно добиться долговечности работы игольчатых подшипников 3000-5000 час.
При изготовлении игольчатых подшипников необходим тщательный отбор игл по размеру. Разность диаметральных размеров не должна превышать 0,002 мм, а в собранном подшипнике должен оставаться общий зазор между иглами от 0,2 до 0,4 диаметра иглы.
Основные формулы для расчета грузоподъемности подшипников качения и их работоспособности известны из курса Детали машин . Кроме того, эти формулы указаны в работе Р. Д. Бейзельмана и В. Б. Цыпкина 4].
Подшипники скольжения
Подшипники скольжения широко применяются в качестве опор валов (роторов) у шестеренных насосов высокого давления. Достоинствами подшипников скольжения, как установлено ранее, являются
малые размеры диаметров и
Разрез по ББ
Г
Разрез по ДЯ
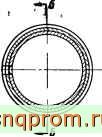
Фиг 44.
относительно высокая нагрузочная способность. Конструктивно подшипники оформляются либо в виде простых цилиндрических вкладышей из антифрикционного материала, которые запрессовываются в соответствующие отверстия корпуса, крышек или уплотняющих деталей (фиг. 44), либо в виде непосредственных расточек в те-ч ле этих же деталей (фиг. 45). Во втором случае эти детали должны быть изготовлены из соответствующих антифрикицонных материалов. При конструировании опор скольжения и расчете минимальной величины зазора должна учитываться наибольшая возможная рабочая температура жидкости.
Если коэффициент теплового расширения материала корпуса больше чем материала втулки, то она должна иметь достаточную величину предварительного натяга (прессовую посадку) с целью предотвращения разбалтывания ее в корпусе при повышении температуры. Если материал корпуса обладает меньшим коэффициентом линейного расширения, чем материал втулки, то при конструировании и расчетах необходимо учитывать соответствующее уменьшение диаметра отверстия с возрастанием температуры жидкости. При окружающей температуре от 12 до 40° С температура чугунного корпуса насоса сохраняется в пределах температуры жидкости.
Если корпус насоса изготовлен из других материалов или когда окружающая температура и температура жидкости меняются в широких пределах, может возникнуть разность температур между корпусом насоса и его внутренними частями. Это непременно должно 104 . I
учитываться при назначении допусков, посадок и зазоров между подвижными и неподвижными деталями насоса. На фиг. 45, а изображена конструкция опорной втулки. Подвод масла к подшипникам осуществляется под давлением 0,6-0,9 кПск через канавку 2. Канавка / предназначена для обеспечения смазки торцовых поверхностей ротора и втулки. Иногда для смазки подшипника предусматривают две канавки, которые располагают диаметрально противоположно. В этом случае смазка подшипников обеспечивается подачей достаточного количества масла при значительной длине втулки.
С целью разгрузки опор от действия радиальных уси- Разрез по RR ЛИЙ в насосах конструкции ЕКМ (ГДР) и ЭНИМС (мод. ГП-1) в каждую из четырех опор валов со стороны нагруженной зоны подшипника подводится масло под давлением, равным давлению нагнетания. Вывод масла в нагруженную зону подшипника производится через отверстие в опорной втулке в точке, расположенной диаметрально противоположно точке приложения усилия, действующего на данную опору. Конструктивное исполнение втулки разгруженного подшипника насоса ГП-1 показано на фиг. 45, б. Здесь: / - канал для подвода масла
из камеры нагнетания к подшипнику, 2 - канал непосредственного подвода масла в зазор между втулкой и валом. Ось отверстия для подвода жидкости наклонена под углом к линии центров, равным углу наклона результирующего усилия действующего на вал. Канавка 3 со стороны, диаметрально противоположной точке приложения усилия разгрузки, соединена со сливом.
На фиг. 44 изображена конструкция опорной биметаллической втулки, примененной в шестеренных насосах конструкции ЕКМ.
Следует отметить, что биметаллические опорные втулки применяются в широком диапазоне насосов конструкции ЕКМ. Тонкий слой (0,8-1 Л1Л1) свинцовистой бронзы центробежным способом наносится на внутреннюю поверхность опорных втулок даже при малых отверстиях втулок (до 15 мм). Применение биметаллических втулок на стальной основе позволяет достигнуть значительной экономии цветного металла и избежать разбалтывания втулок, что имеет место при различии материала втулок и корпуса или других деталей, в которые они запрессовываются.
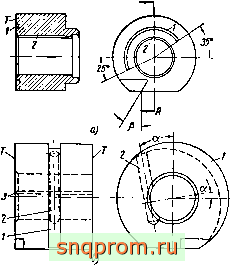
Фиг 45
Указания по расчету подшипников скольжения
Надежность и долговечность работы подшипника скольжения определяется характером трения между его сопряженными поверхностями. Наилучшие условия для работы подшипника создаются жидкостным трением. При этих условиях износ рабочих поверхностей шейки и подшипника происходит лишь в период разгона и торможения, время которых сравнительно невелико.
Жидкостное трение, если оно не исключается величиной нагрузки возможно лишь в том случае, когда поверхности шейки и подшипника разделены непрерывным слоем жидкостной пленки, т. е. при условии, когда
Здесь Ло - толщина слоя смазки в наиболее узком месте зазора; 1 аиб ~ наибольшая высота неровностей на поверхности шейки вала;
гнааб - наибольшая высота неровностей на поверхности подшипника.
Величины и Н^нтб зависят от степени чистоты обра-
ботки в соответствии с ГОСТом 2789-59. Согласно исследованиям П. Е. Дьяченко значения можно представить приближенной
зависимостью:
Я„ = 3,88Я0,
где Н^ - среднеквадратичная отклонения точек профиля, определяемая названным ГОСТом. Следовательно, величина может быть вычислена по формуле
/г„ = 5,4-10-6
> -fl иаи(, + FI
2 наиб
(122)
{D - d) р%
- динамический коэффициент вязкости жидкости в кГсек/мм; число оборотов вала в минуту; диаметр вала в мм;
внутренний диаметр опорной втулки в мм; среднее удельное давление в кГ/см;
коэффициент, равный -LtL.
Величина коэффициента Х принимается в зависимости от соотношений:
Здесь [x п d D Р
Величина коэффициента [х вычисляется по формуле
0,043°Ебо кГсек
(0,U)
,2.6
где t - температура в подшипнике (принимается равной в пределах 75-90° С);
Ебо - вязкость масла в градусах Энглера при Температуре 50° С. Наличие жидкостного трения в подшипнике может быть определено и из зависимости, связывающей нагрузку на подшипник с числом оборотов вала:
С помощью этой зависимости можно установить: при каких соотношениях между усилием Р и числом оборотов сохраняется жидкостное трение.
Для расчета подшипников скольжения при смешанном трении исходят из величины удельного давления р и окружной скорости V. Значения pV для различных подшипниковых материалов указываются в характеристиках каждого антифрикционного материала.
При выборе радиальных зазоров (D - d = А) можно пользоваться следующими ориентировочными зависимостями:
а) для насосов среднего давления при п в диапазоне 1500- 3000 об/мин зазор А должен находиться в пределах 0,002-0,003 от диаметра вала d в мм;
б) для насосов высокого давления при п в диапазоне 1500- 3000 об/мин зазор А должен находиться в пределах 0,0015-0,0025 от диаметра вала d в мм.
При выборе толщины стенок вкладыша (втулки) следует принимать:
а) для чугуна S = 0,03d + 5 мм;
б) для стали S = 0,03d + 3 мм.
Средние допустимые удельные давления для подшипников скольжения принимаются в зависимости от пар трения:
а) сталь по стали 130-250 кПсм;
б) сталь по бронзе 60-90 кПсм;
в) сталь по чугуну 15-25 кПсм.
Отношение внутреннего диаметра втулки D к рабочей длине I зависит от материалов пары трения и выбирается в следующих пределах:
а) для насосов низкого давления 0,9-1,1;
б) для среднего давления 1,1-1,5;
в) для высокого давления 1,3-1,75.
Материалы, применяемые в подшипниках скольжения
Перечень материалов, наиболее часто применяемых для изготовления опорных втулок (подшипников) шестеренных насосов приведен в табл. 4. Там же указаны и марки стали валов, работающих с ними в паре. Мотивы для применения того или иного материала для подшипников насосов идентичны тем, которыми руководствуются при назначении материалов для опор скольжения в других машинах.
Оловянистые бронзы применяются лишь в наиболее тяжелых условиях работы подшипников при удельных давлениях порядка
J07
Таблица 4
Для вала | Для втулки |
Марка стали | Виды термообработки до твердости (по Rq) | Марка материала | Виды термической и химической обработки до твердости (по Н^) |
| В насосах низкого давления | |
40Х 20Х 20Х | Закалка 52-54 Цементация, закалка 56-59 То же | Чугун СЧ 32 52 Чугун антифрикционный Бронза БАЖ | 180-190 190-200 |
| , В насосах среднего давления | |
20Х 20Х 40Х 20Х | Цементация, закалка 57-61 Закалка ТВЧ 54-56 Цементация Закалка 57-61 | Чугун с 1,91% Si, 0,65% Mr, 0,12% Cr, 0,21% Ni, сотыми до лями процента Ti и V и остальным Fe Алюминиевый сплав (АЛ 1.АЛ 16 и АЛ 10) Бронза Бр ОС5-25 Чугун СЧ32 52 | Закалка 190-210 Закалка старение 110-115 Сульфидирование 180-190 |
| В насосах высокого давления | |
12ХНЗА 20Х 38ХМЮЯ | Цементация, закалка 58-61 То же Азотирование 59-64 | Бронза БрОС5 25 Алюминиевый сплав 5-6% Si 3-4% Си, 2-3% Ni, 0,5-1,0% Mg, сотые доли процента Fe, Мп, Sn. Ti Сталь 20Х | Закалка, старение 130-140 Цементация, закалка 57-59 (по Я с) |
1С0 кГ/см и окружных скоростях на поверхности шейки до 5 м/сек. Примерно для таких же эксплуатационных условий применяются и свинцовистые бронзы.
В некоторых иностранных конструкциях насосов высокого давления (175 кГ/см), работающих при 3000 оборотов в минуту приводного вала, применяются оловянистые бронзы, в которые добавляют В качестве присадок серебро (Ag) и берилий (Be). При использовании для опор подшипников различного рода легированных алюминиевых сплавов, В насосах Keela\ite применяются присадки Ni, Mg, Mn, Sn, Си, Fe, S и Ti [28]. Применяя вкладыши из алюминиевых сплавов, следует помнить о их высоком коэффициенте теплового расширения. Это должно быть учтено при определении толщины стенок вкладышей и величины зазора между шейкой и втулкой. Опоры с применением алюминиевых сплавов требуют высокой степени чистоты обработки поверхностей сопрягаемых пар. 108 . ,
При удельных давлениях в пределах 10-20 кПсм и окружных скоростях порядка 2 м1сек употребляются перлитные легированные чугуны марки СЧЦ1 и СЧЦ2. Для обеспечения надежной работы чугунных опор необходимы тщательная отделка трущихся поверхностей и длительный режим их приработки.
Улучшение качества чугунных опор может быть достигнуто применением специальной термообработки - сульфидирования В качестве эксперимента опоры с вкладышами из антифрикционного чугуна, подвергнутого сульфидированию, были установлены на опытном насосе и удовлетворительно работали при удельных давлениях до 40 кГ/см и окружной скорости 3 м/сек. Применение сульфидирования позволило значительно сократить время приработки и улучшить ее условия.
Для насосов низких давлений в качестве опор могут служить различного рода металлокерамические материалы. Однако применение их пока еще по различным причинам ограничено так же, как и применение пластических масс, не прошедших еще необходимой эксплуатационной проверки.
Компоновка опор ведущего и ведомого валов
На фиг. 46 показаны наиболее распространенные конструкции и компоновка опор ведущего и ведомого роторов.
Компоновка опор вала ведущего ротора, изображенная на фиг 46, а, обеспечивает фиксацию вала в осевом направлении (но не фиксирует шестерню). Передний мощный роликовый подшипник рассчитан для восприятия радиальных усилий привода. Грузоподъемность подшипников (в стандартном исполнении) удовлетворяет требованиям опор для насосов среднего давления (до 40кГ/см). Ведомая шестерня вращается на игольчатых подшипниках. При этом внутренние беговые дорожки выполняются на валу (оси), а наружными дорожками служит закаленная шлифованная поверхность отверстия шестерни. Шестерня в осевом направлении сидит свободно в пределах торцовых зазоров.
Недостатком конструкции (а) следует считать применение игольчатого подшипника, который должен изготовляться по 1-му классу точности.
Опорами ведущего и ведомого валов часто являются шариковые двухрядные подшипники широкой серии (фиг. 46, б). Перемещение в осевом направлении вала ведомого ротора ограничивается размерами торцовых зазоров и величиной осевой игры подшипников Ведущий вал этой конструкции не рассчитан на восприятие осевых нагрузок. Недостатком такой компоновки следует считать сравнительно низкую грузоподъемность подшипников, которые возможно вписать в межцентровое расстояние при рациональных размерах шестерен. Компоновка (б) обычно принимается для насосов низкого давления.
Компоновка опор, показанная на фиг. 46, в, позволяет достигнуть жесткой фиксации валов в осевом направлении. Это обеспечивается





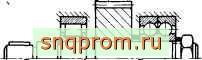
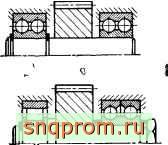





Ведущий вал
(Г


Ведочый вал
Фиг 46 Компоновка опор
1 ...
7 8 9 [
10 ]
11 12 13 ...
18